Posted on February 16, 2023
The production of energetically modified cement (EMC) requires an intensive grinding process. The term "energetically modified" comes from the mechanochemical process used to produce this type of lower-carbon cement.
EMC combines Portland cement with pozzolanic additives like fly ash and silica fume. It is also possible to use natural pozzolans like volcanic rock in the mixes. McKinsey cites EMC’s potential as an energy and emissions saving replacement for ordinary Portland cement (OPC).
When researchers at Sweden's LuleaÌŠ University of Technology (LUT) studied the special cement, they discovered that EMC concrete hardened much faster than certain traditional concrete mixes.
History of EMC
In 1992, LUT’s Vladimir Ronin first used the term “energetically modified cement." In 1996, EMC activation received a gold medal from Eureka, a European research organization. In 1999, construction firm Skanska used fly ash-based EMC to build a bridge in Karungi, Sweden. This was even more notable because of the city's harsh subarctic climate.
From 1992 to 2010, the volume of concrete poured containing EMCs was about 4.5 million cu yd, much of it in DOT projects. To put this in perspective, this is the amount of concrete needed to construct a freeway stretching across America from the Atlantic to the Pacific. It is comparable to the 4.36 million cu yds used to construct the Hoover Dam, its power plants, and related structures.
EMC Activation
Again, EMC activation is a specialized form of mechanical activation. It increases the reactivity of a substance, but without chemical change. Compared to traditional concrete mixes, EMC concrete is as much as 50% stronger.
EMC activation is environmentally friendly as it emits no noxious fumes. The dry, low-temperature process does not require heat, further reducing emissions compared to OPC. Overall, it is a very effective, chemical-free process..
Role of high energy ball milling
High energy ball milling (HEBM) is a mechanochemistry process capable of thermodynamic transformation. It is effective in various forms of nanomaterial synthesis. This specialized vibratory milling process was first used in the concrete industry in 1993.
When used to blend OPC and a pozzolanic additive, HEBM destroys the crystalline structure of a material, making it amorphous. This increases chemical reactivity and surface energy. Since HEBM does not require process heat, it is both energy and emissions efficient.
Energetically Modified Cement: Key Advantages
The most common EMCs feature fly ash, silica fume, or natural pozzolans. It is important to recognize that each kind of EMC possesses its own performance characteristics. For example, EMC formulations impact mechanical load and strength development. Contractors have used EMC concrete for winter concreting, building rehabilitations, and repairs. It is also useful in topping horizontal concrete surfaces, indoors and out. This includes floors and roads.
Replacing OPC for reduced emissions
Energetic modification makes it possible to replace a substantial amount of OPC with one of a variety of supplementary cementitious materials (SCMs). For example, it is possible to replace up to 50% of OPC with fly ash. This is about 2.5 times more than the substitution possible without energetic modification. By extending lifespans, EMC’s durability in extreme and adverse environments also reduces emissions long-term.
Reduced energy requirements
EMC production only requires a fraction of the energy used to produce OPC. In fact, energy consumption of 120 KWh/ton is less than 10% of the energy required to produce Portland cement.
Accelerated strength gain
In testing, the compressive strength of EMC concrete with 20% silica fume increased to twice the strength of a non-EMC formulation. This occurred during early curing at a temperature of 20° C.
High strength and durability
EMC concrete mixes deliver high strength even in adverse environments. Consider these test results from BASF. First, 28-day strength for a 55% replacement of Portland cement with a natural pozzolanic EMC was 14,000 psi / 96.5 MPa.
EMC mixes also performed well in durability testing. In one test, researchers examined a sample saturated in a 7.5% salt water solution. To simulate high diurnal temperature ranges, they also subjected it to 24-hour freeze-thaw cycles.
Self-healing capacity
EMCs promote the healing of microscopic fissures before they become cracks. Effective self-healing could extend the lifespans of certain kinds of concrete structures by years or even decades. Since EMCs are resistant to temperature extremes, self-healing can occur even in frigid arctic temperatures.
Less leaching
In 2001, LTU researchers performed leachability tests on EMC concrete formulated with fly ash. The results confirmed low surface specific leachability. EMC concrete mixes also resist efflorescence. This occurs when calcium hydroxide from within the concrete reacts with CO2 in the air.
Potential for customized mixes
It is possible to custom design concrete with EMCs. For example, one can emphasize strength, or rapid hardening, or both. One high-strength EMC concrete achieved 70 MPa/10,150 psi in 24 hours.
EMC Projects
In the United States, EMC is approved by the Federal Highway Administration. EMC is also certified for use by various state transportation agencies. This includes major ones like TxDOT, CalTrans, and PennDOT.
EMCs meet the requirements of a variety of technical standards that apply in the United States and abroad:
ASTM C618-19 (U.S.)
EN-197, EN-206 and EN 450-1:2012 (CEN nations)
BS 8615‑1:2019 (U.K.)
About PACA
The Pennsylvania Aggregates and Concrete Association (PACA) reports industry news and innovations through this website. The team at PACA welcomes any questions you may have about your current or upcoming concrete project. Please contact us at your convenience.
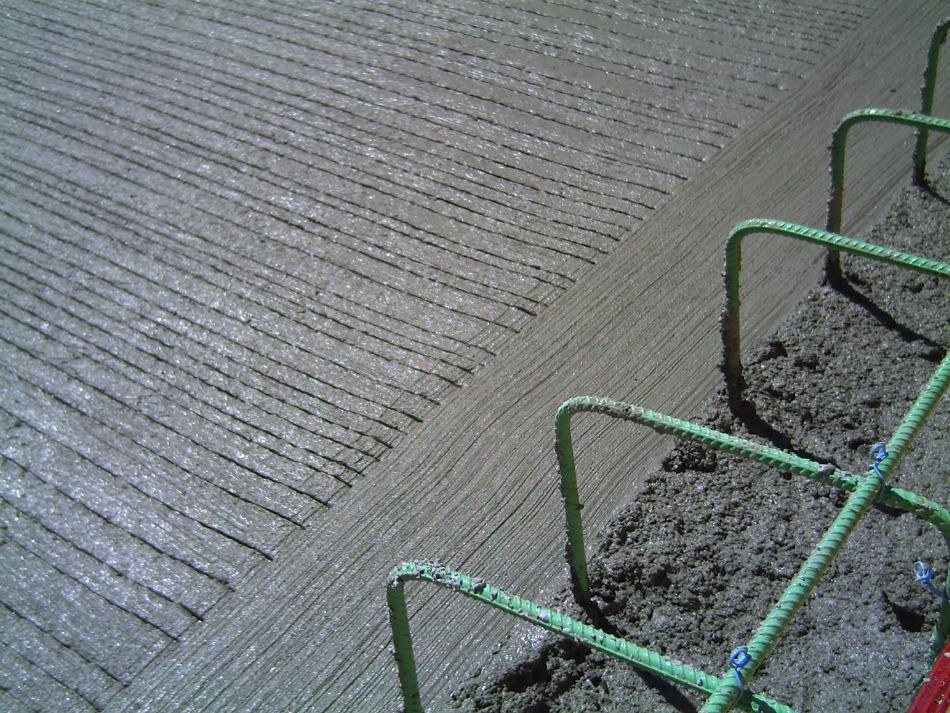