Posted on February 22, 2024
Proficient carbon calculations are increasingly important as “Buy Clean” legislation proliferates. New York and Colorado are among the states that now require carbon calcs for public projects.
An estimated 40% of emissions are from the built environment. According to one estimate, the planet’s total building floor area will double by 2060. This makes the concrete industry a key player in the quest for net-zero emissions products and projects.
What is Whole-life Carbon?
Whole-life carbon calculations feature comprehensive cradle-to-cradle analysis. This includes raw extraction, processing, product creation, and transportation. It includes every aspect of the cycle, including sales and distribution. Whole-life carbon calculations also include end-of-life scenarios like concrete crushing and recycling.
It is the sum of embodied carbon and operational carbon. Together, embodied and operational carbon constitute the more valuable metric, whole-life carbon.
Embodied carbon
Embodied carbon includes CO2 emissions from all materials and construction processes. It also includes the later demolition and disposition of the structure. Ideally,this includes recycling of much of the material.
Reducing clinker intensity is one way to reduce embodied carbon in the concrete industry. For example, Portland limestone cement (PLC) reduces emissions about 10%. Supplementary cementitious materials (SCMs) reduce emissions up to 30% and more. These include emerging SCMs like calcined clay and glass pozzolans.
It is also possible to substitute other materials for calcined limestone, like calcium silicate or magnesium oxide (from magnesium silicate). Bio-concrete is another possibility. Advanced technologies that increase binder efficiency also reduce clinker volumes.
Governments increasingly address the embodied carbon of future construction. Consider California’s AB 2446, for example. The law requires a 40% reduction in embodied carbon in the state’s construction by 2035. A recent update requires calculations of embodied carbon in 100,000+ sq ft commercial buildings. The same standard applies to 50,000+ sq ft schools. Compliance may occur in one of three ways:
Reduce a project’s total embodied carbon by 10%
Meet emissions benchmarks of the projects various building materials used
Reusing 45% or more of an existing building
Operational carbon
Through 2050, embodied carbon will comprise half the carbon footprint of new construction. Operational carbon will account for the other half. Operational carbon is from 1) use of the asset, 2) maintenance, and 3) refurbishment. It includes the emissions associated with heating, cooling, and lighting it.
Concrete’s thermal mass helps to reduce operational emissions. For example, insulated concrete forms (ICFs) effectively combine thermal mass and continuous insulation.
As Logix ICF notes, “The combination of the thermal mass of concrete, and high insulation value of the form panels, has an effect of creating an R-value of the wall assembly that can be greater than the tested R-value of the insulation. This is the “effective R-value” of ICFs.
The impact on heating and cooling varies per the Climate Zone Map in ASHRAE 90.1. Areas with high cooling loads benefit the most. Most of Pennsylvania lies in zone 5, with some zone 6 areas across the northern part of the state. Thermal mass effect benefits are less pronounced in Pennsylvania than in zones 1-4.
Carbon Reduction Design Tools
Various tools assist architects, engineers, and designers as they strive to reduce the whole-life carbon of their designs.
Embodied Carbon in Construction Calculator
The Embodied Carbon in Construction Calculator enjoys wide acceptance in the concrete industry. "EC3" focuses on emissions associated with construction materials. The no cost, cloud-based tool now boasts more than 15,000 users. It offers key benefits, including the standardization of metrics to enhance analysis.
The EC3 tool acquires data from BIM and/or construction estimates. This information gets matched to Environmental Party Declarations (EPDs). Stakeholders can make better sourcing decisions, on a line-by-line basis. As UL notes, an EPD “tells the life cycle story of a product in a single, comprehensive report.” It quantifies adverse environmental impacts like smog, water pollution, ozone depletion, and more.
MIT’s carbon uptake tool
MIT’s Concrete Sustainability (CS) Hub offers its whole life cycle carbon uptake tool. The tool is a “state-of-the-art, material- and facility-specific calculator for carbon uptake in concrete.” It accounts for carbonation at various stages of the life cycle, including possible stockpiling of recycled concrete aggregates (RCA). The calculator considers important variables at a granular level, including concrete mixtures, exposure characteristics, and stockpiling conditions.
Carbonation strengthens concrete while permanently sequestering atmospheric CO2. It is a chemical reaction between calcium hydroxide (Ca(OH)2) in concrete and atmospheric carbon dioxide (CO2) that yields calcium carbonate and water. It is a slow, ongoing process that begins at the surface and works its way inward. Carbonation only happens with exposed, unsealed concrete.
Globally, carbonation now offsets 43% of emissions from current cement production.
Other strategies
Many ways exist for designers, contractors, and other industry professionals to reduce the carbon footprint of their projects. Government also has a role to play. Regulating public procurement is a cost-effective way to promote the use of low-carbon products. Various states already have low-carbon procurement policies in force. New York, New Jersey, Colorado, and Oregon are examples.
Taking Action to Reduce Whole-life Carbon
There are a variety of ways designers and builders can maximize the whole-life carbon benefits of concrete structures. Lean building design is one example. For example, both ultra-high-performance concrete (UHPC) and graphene concrete allow for leaner, lighter designs. It is also possible to extend the already long lifespans of concrete buildings by specifying concrete mixes offering better performance for the intended use.
Given the carbon intensity of new concrete, it is often better to reuse an existing structure. As The Concrete Centre asserts, “Concrete buildings also offer a level of flexibility not found in many other structural options, frequently enabling them to be repurposed to meet changing needs, greatly extending their useful lifespan.” In some instances, reusing concrete structures diverts material from landfills.
About PACA
The Pennsylvania Aggregate and Concrete Association (PACA) reports on the latest developments in the industry. Do you have a project in the works? If so, our team welcomes your concrete-related questions. Contact us at your convenience!
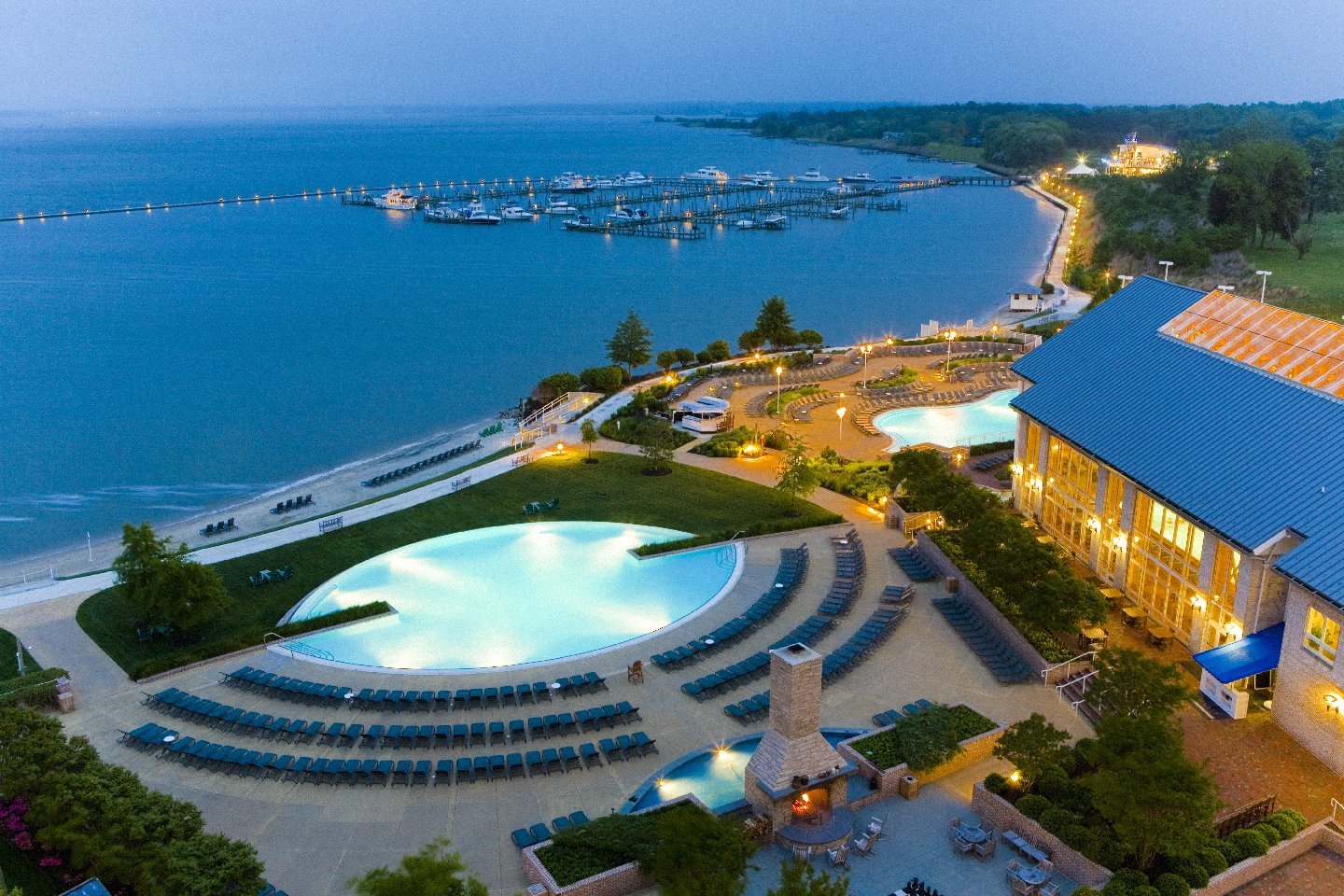