Posted on October 27, 2022
In the span of only 150 years, reinforced concrete became one of the world's most significant building materials. The roads we drive on, the buildings where we work, and the homes we live in all rely on the strength of reinforced concrete.
Today, the quest for performance is balanced with the pursuit of lower emissions. Everything is viewed through these twin lenses. Industry innovation includes reinforcing concrete in more sustainable ways. At the same time, better reinforcement often means less concrete for a given application. In essence, better performance can reduce emissions.
The history of concrete spans millennia. More than 2,000 years ago, Roman engineers designed concrete seawalls that remain to this day. The secret? The strengthening effect when the saltwater reacted with the concrete.
By contrast, rebar reinforcement is in its infancy. In 1867, Frenchman Joseph Monier received a patent for his rebar design. Soon thereafter, rebar arrived in the United States. In 1878, the U.S. Patent Office granted Thaddeus Hyatt a patent for his reinforced concrete.
By the early 1900s, the use of rebar was common throughout the country. Reinforced concrete overcame the height limitations of wood and the prohibitive cost of quarried stone.
Traditional Rebar: Shortcomings
Reinforcement addresses concreteās lack of tensile strength. However, cost effective iron and steel are ferrous metals vulnerable to corrosion and rust. Author Robert Courland ponders the results if the Romans had built Spain's famous Alcantara Bridge with such rebar. He estimates it would have been rebuilt at least 16 times by now. .
There are two main causes of chloride-induced corrosion in rebar. One is the use of deicing salts in cold climates. The other is salt exposure in marine environments. When concrete undergoes alternate wetting and drying, chloride-laden water penetrates the concrete. This is often referred to as a chloride attack. One answer is to use concrete with low permeability. It resists chloride ion ingress and other threats. Another answer is the use of corrosion-resistant rebar.
More Sustainable Alternatives
Emerging alternatives to steel rebar offer key advantages. First, they eliminate the threat of corrosion and rust. Second, they weigh less, making them easier to handle at the jobsite.
Fiber-reinforced polymers (FRP)
Dr. Antonio Nanni is a University of Miami engineering professor who observes that āFRP rebar is ready for prime time.ā What is needed is for more designers and engineers to specify it and for more contractors to use it. Popular reinforcers include glass fiber, carbon fiber, and basalt fiber.
Glass fiber reinforced polymer (GFRP) is 2-4 times stronger and 4-7 times lighter than steel. When combined with stainless steel ties, GFRP offers key rust and corrosion resistance. Accordingly, GFRP rebar has found early acceptance in sea wall and bridge construction. However, GFRP rebar is not always an acceptable substitute for steel. Although it has a higher tensile strength, it demonstrates a lower tensile modulus.
By weight, GFRP may be as much as 3-4 times more expensive than steel. By volume, however, it is cost competitive. This is particularly true when one factors in its performance parameters. One example is GatorBar Glass, a GFRP rebar manufactured by Neuvokas Corp. In 2022, the Virginia Department of Transportation (VDOT) included it on its New Product Evaluation List.
Composites World describes the use of GFRP rebar at a flood control project in Jizzan, Saudi Arabia. Project managers used three GFRP suppliers for the massive endeavor.
Carbon fiber reinforced polymer (CFRP) rebar is similar. It too is both strong and lightweight. It is also thermally and electrically non-conductive. It is also useful in the presence of strong magnetic fields. One example is flooring beneath MRI medical equipment.
Like its GFRP counterpart, CFRP rebar is also impervious to chloride ion and chemical attacks. It is employed as a steel substitute in a wide variety of applications. Examples include bridge decks, parking garages, office buildings, and shopping malls.
Basalt fiber reinforced polymer (BFRP) is yet another option. Designers already specify BFRP in a variety of construction, automotive and military applications. The supply of raw material is not in question. Consider that 90% of all volcanic rock on the planet is basalt. To fabricate BFRP, the rock gets melted down and drawn into a continuous fiber spooled on a bobbin. The fiber and a polymer matrix combine to form yet another advanced rebar product.
Engineered bamboo
Bamboo is the fastest-growing tree on the planet. Hardwood trees take 40+ years to mature. Compare this to bamboo. Depending on the species, bamboo is ready to harvest in one to five years. Bamboo, like other plants, pulls carbon dioxide from the atmosphere. This makes bamboo rebar capable of carbon sequestration. However, bamboo rebar must be formulated so it does not rot or succumb to bacteria or fungus.
In response, fabricators make woven strand bamboo (WSB) by slicing skinned bamboo stalks lengthwise. The thin strips get carbonized and dipped into a water-based adhesive. They get placed in molds and pressed under pressure. The process yields rebar with triple the density of natural bamboo.
In Alberta, Canada, three engineering students designed a modified bamboo product injected with an elastomeric polymer. Their bamboo rebar is a sustainable alternative to steel rebar for low-load applications. Research remains to determine if larger diameter bamboo will work in high-load environments.
Micro Rebar
In the right applications, micro rebar reinforcement is an alternative. Reforce Tech, a Norwegian company, produces BFRP āBasBars.ā Basalt fibers get wrapped with polymer resin in a helical shape. Micro rebar does not impair workability when added to concrete mixes. They do not protrude from finished surfaces.
USA-made Helix Micro Rebar is inch-long twisted steel. It infuses and therefore reinforces every part of a pour. Superior crack resistance is one advantage, while workability is another.
About PACA
The Pennsylvania Aggregates and Concrete Association (PACA) informs its members and the public about industry innovation. The team at PACA welcomes any questions about your upcoming concrete project. Please contact us at your convenience.
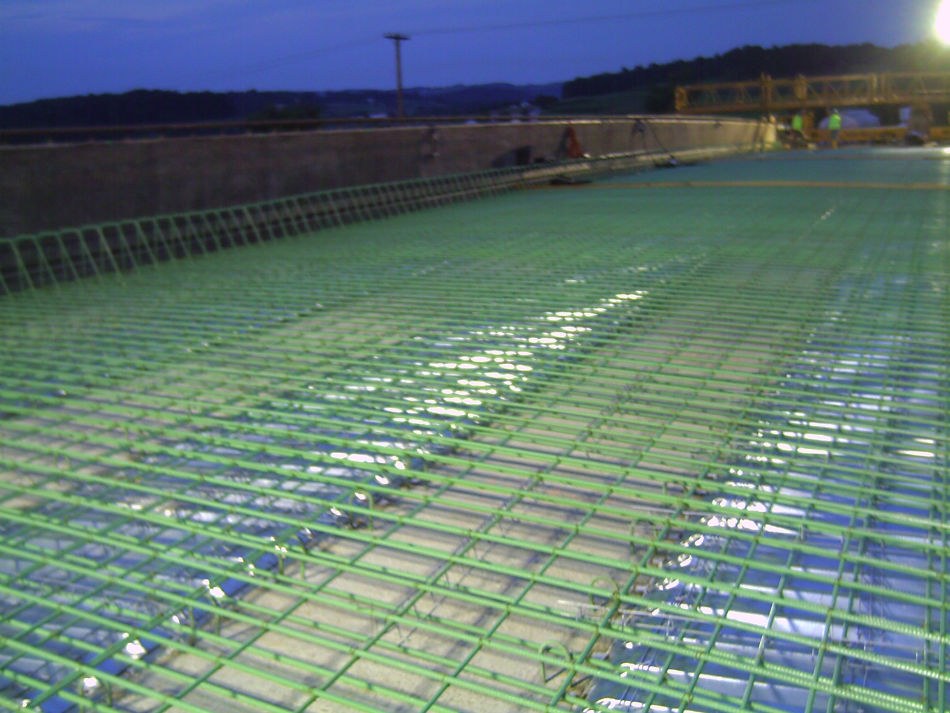