Posted on December 08, 2023
Cement kilns are a two-pronged source of carbon emissions. Traditionally, fossil fuels heat cement kilns to the required temperatures. In turn, this heat breaks down limestone and other carbonate-rich materials, releasing carbon dioxide in the process.
To monitor the process, the Environmental Protection Agency (EPA) requires cement plants to comply with its Greenhouse Gas Reporting Program (GHGRP). Every year, plant representatives must report:
Clinker production
Cement production
GHG emissions
In 2019, 92 U.S. cement plants reported a total of 67 million tons of carbon dioxide equivalents (CO2e). This is a significant amount. The EPA says, “These emissions comprise roughly 10% of the industrial sector’s direct reported emissions.”
Accordingly, the industry continually looks for ways to reduce emissions. Examples include: alternate fuels, supplementary cementitious materials, and new operational methods.
Cement Kilns: Quest for Fossil Fuel Alternatives
Fossil fuel alternatives range from hydrogen to recycled waste. Electrically powered heat sources are also contemplated, including plasma torches.
Electrically generated plasma torches
A plasma arc torch concentrates a flow of high-temperature plasma toward a target. Common uses include: plasma arc welding, plasma cutting, and toxic waste disposal. In arc welding, the main parts are the electrode, swirl ring, and nozzle. A swirl ring isolates the electrode and from the nozzle. It has vent holes that help create a swirling vortex of plasma.
High-power plasma torches have been around since the late 1940s. At that time, Chemische Werke HĂĽls AG deployed an eight megawatt torch to synthesize acetylene from coal. Plasma torches also generate the high temperatures required to decompose GHG and PFC pollutants.
Now, Swedish researchers believe there’s another use for the equipment. They want to replace a kiln’s coal-fired flame with electrically generated plasma one. Plasma torches achieve temperatures of 3,000º C. By contrast, conventional coal-fired kilns reach about 1350-1450º C. Plasma torch technology either runs on electricity from the grid or from energy stored in batteries. These devices are also effective when used with recycled waste - a big plus.
Simulations used in Matlab determine whether it is possible to sustain the required temperatures. Simulations help researchers better understand how sensitive the process is to changing variables.
Will plasma torch technology work for extended periods in cement kilns? One study suggests that it can. It is also possible to treat high-temperature plasma to treat GHG gasses. Researchers analyzed the discharge characteristics, thermal efficiency, and durability of the plasma torch. The drive performed successfully for more than 1,000 hours. It overcame extreme temperatures, turbulent flows, and vibration. A molybdenum preserve nozzle overcomes electrode erosion that shortens a torch’s lifespan.
The University of Florida’s UF Innovate is the home of another plasma torch project. An abstract from the patent application details the operation of the proposed plasma arc gasification kiln. In one example, a plasma plume with argon gas reaches temperatures of 1800-3000º C. In another example, a plasma arc gasification kiln receives raw meal and heats it in an early stage of clinker production.
Plasma torch tech eliminates the clinker contamination ordinarily associated with fossil fuel combustion.
Alternate Fuels
Cement plants continue to look for cost-effective alternatives to fossil fuels. For example, Heidelberg says it can get more than 90% of the thermal energy required in kilns “using secondary fuels.” In Europe, refuse supplies about half the fuel used by kilns.
According to a McKinsey report, “The cement plant of the future could reduce emissions by up to 75 percent by 2050. However, the availability of alternative fuels varies by region. Also, it depends on the decarbonization efforts of sectors like steel and energy. The same holds true for clinker substitutes, including natural pozzolans or industrial byproducts.
Let’s take a look at various alternatives to fossil fuel.
Biomass
Biomass may consist of dried sewage sludge, waste wood, or industrial waste. A number of major cement manufacturers have committed to substantial increases in the use of biomass. For example, Heidelberg seeks to increase the percentage of biomass used as fuel from 9% in 2020 to 19% in 2030.
Recycled plastic
There's also untapped potential in the use of recycled plastic to fuel kilns. The need is great. Projections suggest that plastics production will double in the next 20 years. According to Pew Charitable Trusts, the weight of plastics flowing into the oceans could triple by 2040.
Historically, the plastics recycling rate averages less than 10%. As Geocycle CEO Axel Pieters asserts, “burning plastic in cement kilns is a safe, inexpensive and practical solution.” In Indonesia, contractors unearth plastics in landfills to burn as kiln fuel. Geocycle, a Holcim subsidiary, uses 2 million tons of plastic waste per year at cement plants. By 2040, it hopes to consume 11 million tons per year.
Hydrogen injection
Hydrogen injection reduces cement plant emissions by 3-5%. Cemex started injecting hydrogen in 2019. It expects to retrofit all its European plants with the technology. In 2022, Argos Honduras tested the injection of hydrogen into a cement kiln. It split water via electrolysis before injecting the resulting hydrogen and oxygen directly into the kiln’s main burner.
In 2021, a Heidelberg Cement subsidiary in the UK ran a successful trial using hydrogen as part of the fuel mix at a plant in Ribblesdale. Operators achieved 100% alternative fuel by combining hydrogen with bone meal and glycerine.
Prospect of Costly Conversions
It is often expensive to retrofit cement plants to operate with new fuels and technologies. For example, McKinsey estimates an alternative fuel installation at a cement plant may cost $20 million. It can take a year to commission the upgrade and to get online.
A 2019 feasibility study looked at the cost to convert a cement plant in the UK so it could use hydrogen instead of fossil fuels. Upgrading a kiln burner, adding hydrogen storage and pipework costs 400,000 Euros or so. This cost is somewhat offset by eliminating the cost of carbon capture, utilization, and storage (CCUS).
Future of Cement Plant Innovation
To achieve looming carbon neutrality goals, cement plant innovation must continue. Areas of interest include: advanced analytics and Industry 4.0 efficiencies.
Advanced analytics
Conventional pyroprocessing is a fuel-intensive process that traditionally relied on fossil fuels. The resulting clinker consists of small lumps of stony residue which are ground into a powder. It is blended with other ingredients to produce commercial-grade Portland cement.
Advanced analytics (AA) could make a significant contribution to the quest for carbon neutrality.
McKinsey asserts that, “AA algorithms improve yield, throughput, quality, energy efficiency, and cement-to-clinker ratios.” Automated tracking of overall-equipment-effectiveness (OEE) loss and AA-enabled software tailor asset strategies improve equipment reliability.
Industry 4.0 efficiencies
McKinsey cites the possible savings. Applying digitization and sustainability “levers” to cement production could reduce prices $4 to $9 per ton.
About PACA
The Pennsylvania Aggregate and Concrete Association uses SpecifyConcrete.org to inform its members and the general public of industry innovation. The team at PACA welcomes questions about your upcoming ready-mix project. Please contact us at your earliest convenience.
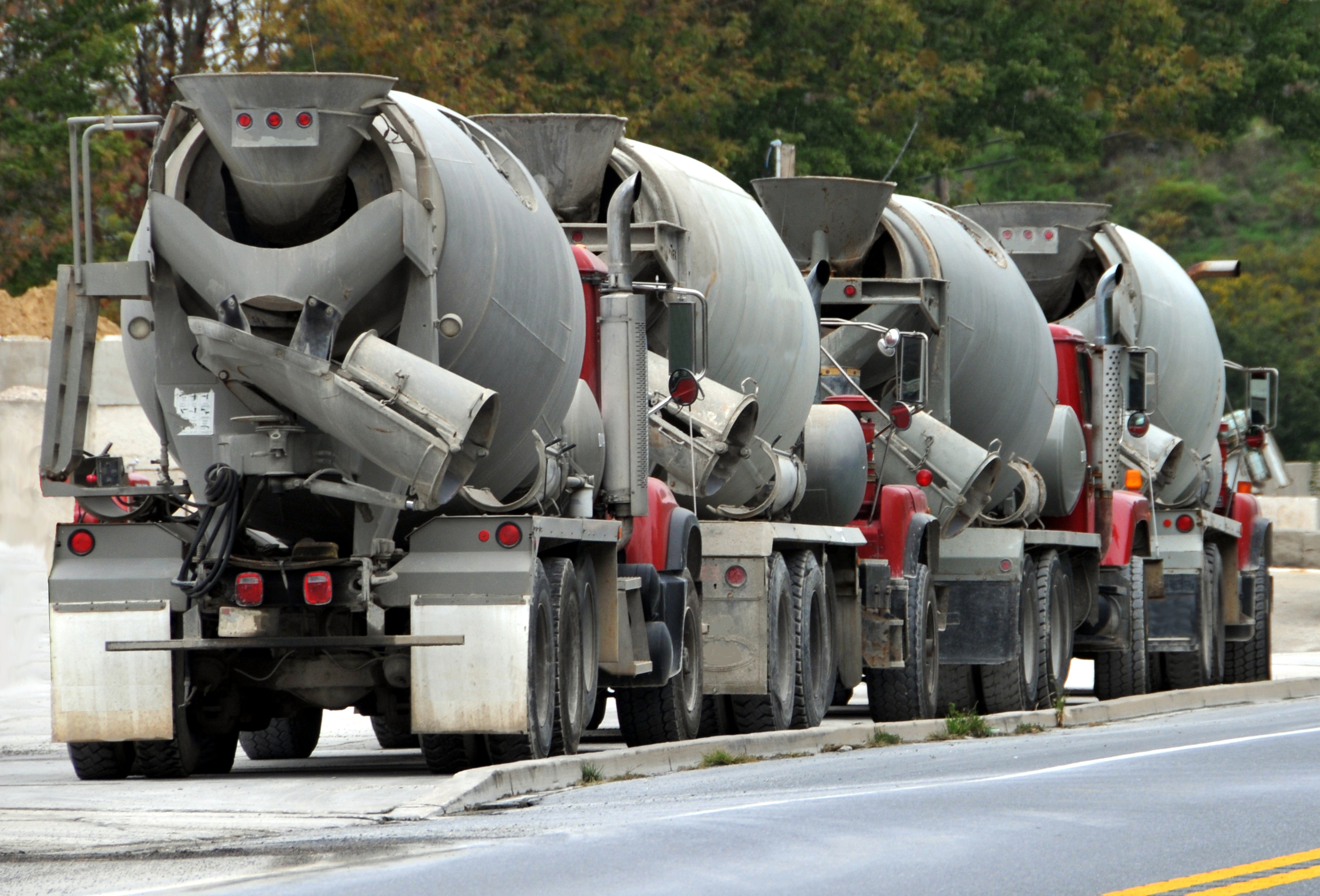