Posted on March 16, 2023
There are circumstances when the air around us is simply not good enough – times when more concentrated oxygen works wonders. For example, oxygen aids climbers during ascents of Mount Everest. Oxygen also aids spent football players as they rest along the sideline.
Similarly, good things happen when cement kilns breathe oxygen instead of ambient air.
The Oxyfuel Process
In the so-called oxyfuel process, kiln combustion occurs with pure oxygen rather than air. An air separation unit (ASU) delivers the required oxygen to the cement kiln. A big advantage of the oxyfuel process is the purity of the flue gas. Unlike the emissions from traditional kilns, the resulting exhaust fumes are mostly devoid of non-CO2 gasses. Josh Lemke, a process engineer at thyssenkrupp Polysius, explains, “Due to the high concentration, we can separate and capture almost 100% of the climate-damaging carbon dioxide instead of allowing it to escape unhindered into the atmosphere.”
To capture the CO2, all that is necessary is the removal of water vapor and minimal impurities in a compression and purification unit (CPU). This leaves CO2 that’s ready to transport and use or store. Alternatively, it is possible to recirculate flue gasses back into the system.
In response to this promising oxyfuel technology, sophisticated research continues. At SINTEF Energy, data from an oxyfuel pilot project will be used to run a Computation Fluid Dynamic (CFD) simulation of a full-scale rotary kiln. SINTEF is one of Europe’s largest independent research organizations.
Maxwell Pisciotta, a PhD candidate at Penn’s Clean Energy Conversions Laboratory, touts the emissions-saving potential of the oxyfuel alternative. He estimates that a full conversion from traditional coal-fired kilns to oxyfuel kilns could reduce CO2 emissions by two million Mt/yr.
Full vs. partial conversions
Two different concepts are under development: full and partial oxyfuel. Each approach offers distinct advantages. Converting to 100% oxyfuel delivers CO2 capture rates of more than 90%. However, it requires more comprehensive alterations to the production process. While the partial oxyfuel option delivers lower capture rates (55-75%), it requires fewer changes. Cement manufacturers can also choose a staged implementation of oxyfuel tech.
Evolving technology
The original oxyfuel concept involved mixing flue gasses with oxygen before recycling them to the main kiln burner to control the temperature.
In second generation oxyfuel systems, excess oxygen controls the temperature in the main kiln burner. The excess oxygen is further consumed in the calciner downstream from the kiln. Rather than being recycled, the CO2 in the flue gas is directly captured for transportation and reuse. This allows for the use of more compact and less expensive equipment. Despite the capital investment and the power requirements, oxyfuel + carbon capture is one of the best paths to carbon neutral cement plants.
Oxyfuel Kilns: Challenges
There are several issues to be overcome for oxyfuel kilns to gain wide acceptance. First, the intrusion of ambient air into the process quickly decreases efficiency. Therefore, it is important to consider the expense of installing and maintaining a leak-free system. Required changes to burner and cooler designs also increase costs.
Second, the oxyfuel/carbon capture combination doubles the electricity required. This increases costs about 40% to 50%. Use of renewable energy reduces the environmental impact of this increased power usage. Finally, the cost of production line retrofitting is also a challenge. Fortunately, a graduated retrofit is possible, with a conversion coming in stages over a period of years.
Case Studies
The industry’s acceptance of new tech is reflected in its willingness to proceed with pilot projects. Decision makers are moving forward with multiple oxyfuel projects in Europe.
Catch4Climate
Catch4Climate is a project of Cement Innovation for Climate (CI4C). The oxyfuel pilot project is slated for Schwenk Zement’s Mergelstetten plant in Germany. It is a collaborative effort of Vicat, Dyckerhoff, Heidelberg, and Schwenk Zement.
The plant will devote one production line to the oxyfuel process. The $127 million project will have a 450t/day capacity, with production commencing in mid-2024. CO2 captured in the process will help to produce synthetic aircraft fuel. When renewable energy powers this process, the resulting “reFuels” will be climate neutral.
Anthemis
In January 2023, Heidelberg announced plans to implement its OxyCal concept at a Belgian cement plant. OxyCal is a hybrid technology combining oxyfuel and amine capture. Heidelberg estimates that the process will capture about 800,000 tons of CO2 per year. This will reduce the cement plant’s carbon footprint by 97%. Heidelberg seeks partners for help with transportation and storage of the captured carbon. The plant will produce an estimated 15 million tons of carbon-neutral cement during its first decade of operation.
The innovative 2nd-gen design eliminates the need for an additional preheater tower. This saves a considerable amount of structural steel and concrete in the process.
Carbon2Business
Carbon2Business is one of four cement projects receiving money from the European Union’s Innovation Fund. In July 2022, Holcim announced plans to install a 2nd gen oxyfuel kiln at its plant in Lagerdorf, Germany. An air separation unit delivers oxygen directly to the kiln. Due to the purity of the CO2 emitted, it can be directly captured and liquefied. Annual carbon capture will total 1.2Mt/yr, making the plant carbon neutral. The captured CO2 will serve as feedstock for a chemical plant producing methanol.
About PACA
The Pennsylvania Aggregates and Concrete Association (PACA) reports on industry developments at SpecifyConcrete.org. PACA’s staff welcomes questions about your next concrete project. Please contact us today!
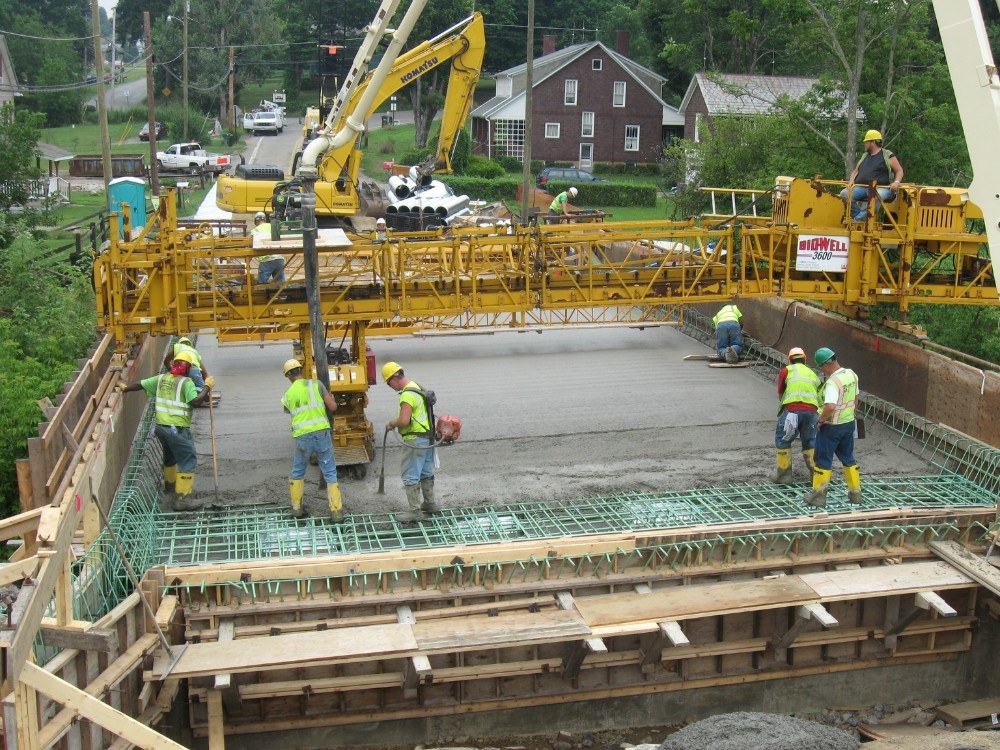