Posted on December 01, 2023
Concrete is everywhere. By mass, it represents more than half of all manmade materials produced annually. Unfortunately, the Portland cement used as a binder is emissions-intensive. Global cement production totalled 4.1 billion metric tons in 2022. Just over half of that came from one country - China. On average, U.S. clinker production is responsible for about 842 kg of CO2 per ton of Portland cement produced.
One of the ways to reduce cement’s carbon emissions is simple but elusive; replace some energy-intensive clinker with limestone. Fortunately, there’s no need to compromise performance in making this substitution. As the Portland Cement Association (PCA) notes, “Portland-limestone cement (PLC) is a blended cement with a higher limestone content, which results in a product that works the same, measures the same, and performs the same, but with a reduction in carbon footprint of 10% on average.”
In short, PLC speeds the transition to more eco-friendly concrete. This transition has accelerated to the point that ordinary Portland Cement (OPC, per ASTM C150) will no longer be available in the near future.
Overview of Portland Limestone Cement (PLC)
PLC (Type IL) is a durable and resilient alternative to ordinary Portland cement (OPC). It is possible to deploy it as a 1:1 replacement. It is another step in the evolution of Portland cement, a product patented 200 years ago.
Incorporating ground limestone into cement is not a new idea. Some European cement plants already used it in the 1960s. Canada approved its use in 1983. Producers optimize PLC with finer grinding to enhance the performance. The finer particles pack closely together, reducing permeability. Intergrinding of limestone and Portland cement clinker further improves performance.
By common definition, OPC contains up to 5% limestone while PLC contains 5-15%. Once research confirmed PLC’s viability at replacement levels exceeding 5%, the Canadian standard changed to 15% in 2008. In 2012, ASTM C595 also set a 15% maximum. Above 15% replacement, problems arise. Slower set times, reduced strength, and increased porosity are common challenges.
Quest for >15% concentrations
There is hope that replacement levels could still exceed 15%, further reducing emissions. Researchers are looking at synergies between the limestone and alumina-rich SCMs. In one study, researchers examined resistance to sulfate penetration and leaching at higher concentrations
It is still possible to incorporate a variety of pozzolans without undermining the benefits of the limestone. Two common examples are fly ash from coal-fired power plants and granulated slag from steel plants.
Limestone particles enhance hydration, although interparticle distance is a critical variable. Finely ground limestone increases shearing between particles, multiplying C-S-H nucleation sites. As one researcher notes, “C-S-H tends to nucleate preferentially on the surface of the limestone particles, which further accelerates hydration.”
Rapid Adoption of Portland Limestone Cement
PLC use expands as building codes address it and major agencies accept it. The Portland Cement Association documents state-by-state DOT acceptance of PLC here. The American Institute of Architects (Master Spec) and the Federal Aviation Administration (FAA) also accept PLC.
Codes also aid the PLC transition. ACI 301, “Specification for Structural Concrete” references PLC. ASTM C94, “Specification for Ready Mixed Concrete”, treats PLC like other blended cements. For more than a decade, U.S. standards ASTM C595 and AASHTO M 240 recognized PLC. Canadian standard CSA A3001 does as well.
ACI 318, “Building Code Requirements for Structural Concrete,” addresses OPC and blended cements like PLC. Lacking sufficient testing, ACI 318 does not address design criteria and performance. This means that PLC often requires approval by licensed design professionals.. Materials suppliers and concrete producers must conduct testing that yields the desired data. For more ACI 318 resources, click here. Also, check out the PLC fact sheet published by the PCA.
In terms of emissions, the switch to PLC is significant. In the United States alone, full adoption would be the equivalent of taking 1.75 million cars off the road.
Future of Lower Carbon Cement
Producers, associations, and governments are all adopting “zero carbon by 2050” strategies. This means that the quest for new concrete mixes will only intensify.
Advanced limestone strategies
Researchers continue to look for ways to use blended cements with more than 15% limestone. One way to accomplish this is through finer grinding. It is also possible to reduce emissions by up to 70% by using so-called “carbon-negative limestone” produced with waste CO2.
Basalt instead of limestone
Other researchers look at replacing limestone with basalt. Research establishes that basalt improves long-term compressive and flexural strength while enhancing durability. In one study, researchers replaced 7.5, 15, and 22.5% of Portland cement with basalt. They found that 15% was the optimal basalt replacement level. At 22.5%, compressive strength suffered.
Use of oxygen-rich air
Another strategy involves the use of oxygen-rich air to dry raw meal before it goes into the kiln. Raw meal requires the crushing and subsequent milling of quarried limestone and/or gypsum. It is usually heated to about 700º C in a chamber above the cement kiln. The kiln’s hot gasses drive off moisture. By introducing oxygen-rich air, it is possible to cut emissions as long as the remaining CO2 is captured.
About PACA
The Pennsylvania Aggregate and Concrete Association welcomes this opportunity to inform its members and the general public of industry innovation. The team at PACA will field your questions about your upcoming ready-mix project. Please contact us at your earliest convenience.
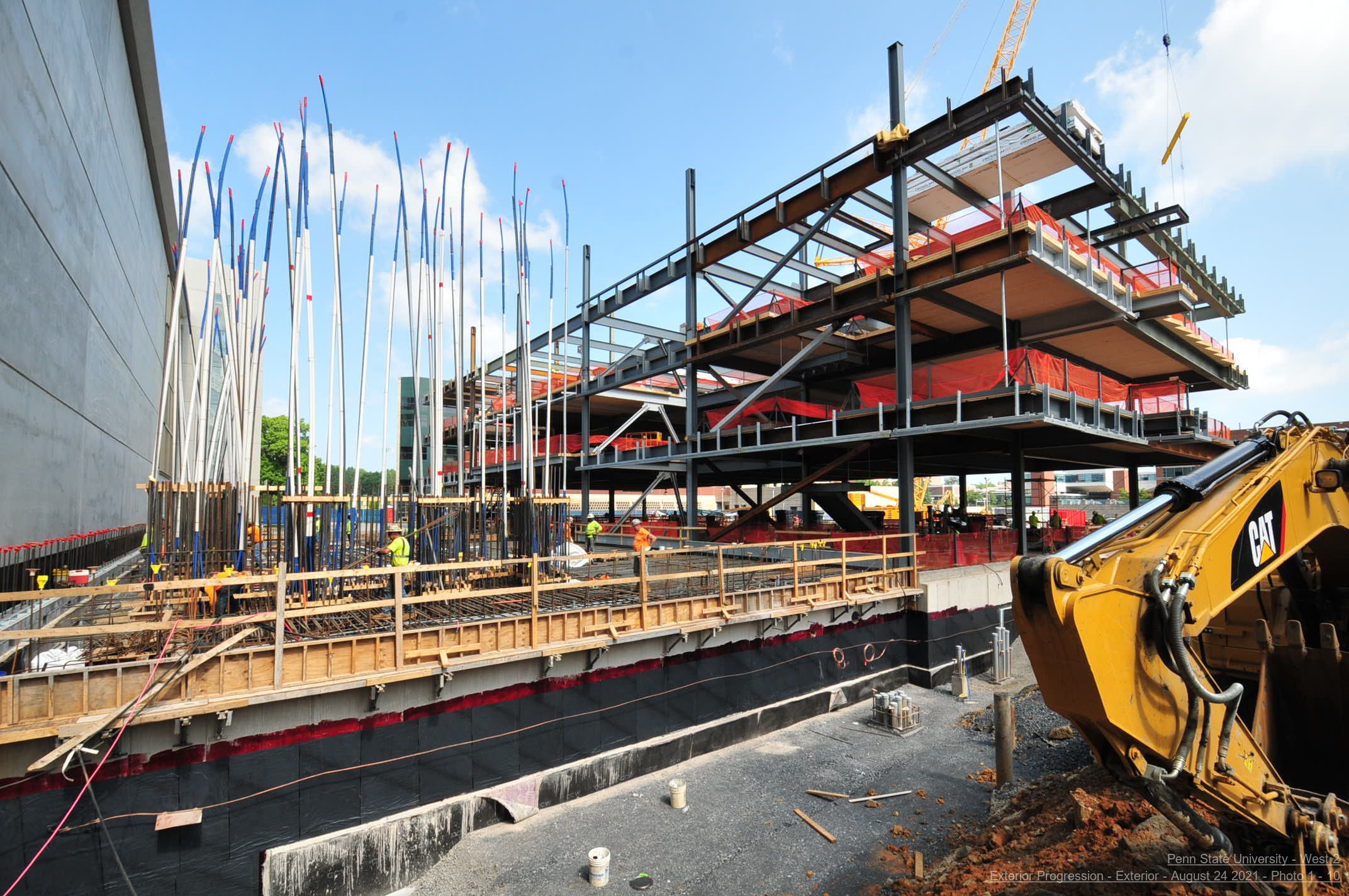