Posted on September 17, 2020
In important ways, the future of the planet depends on better balancing the emission and absorption of carbon dioxide (CO2). For example, forests absorb CO2, making them effective carbon sinks. By specifying concrete over wood, designers protect unlogged forests.
Turns out, forests are not the only significant carbon sinks. Thanks to carbonation, concrete absorbs about 25 percent of the carbon absorbed by the world’s forests.
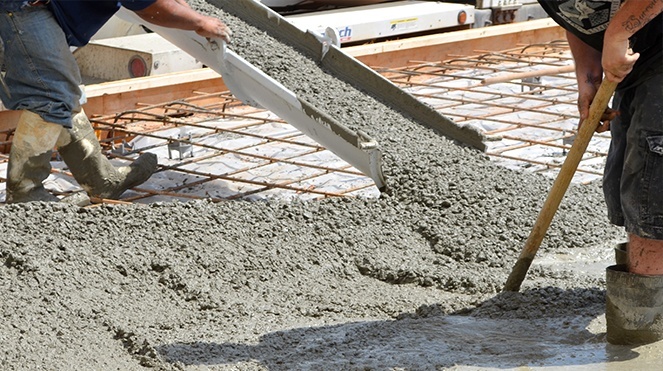
Carbonation Offsetting Calcination
A 2016 study calculates that “43 percent of cement-based emissions generated between 1930 and 2013 have been sequestered by cementitious materials within that same time period.” In 2013, “cementitious materials absorbed roughly 2.5 percent of global carbon emissions.” The environmental impact of concrete may be as little as half of what it was originally thought to be.
Architect magazine suggests that concrete “might not be as detrimental to the environment as once believed.” Architects who practice “carbonation awareness” maximize CO2 absorption in aging concrete. That is, “minimize surface treatments that prohibit this chemical weathering.”
For example, the Mosler Lofts in Seattle, WA, feature a great deal of exposed concrete. The designers left concrete columns, core walls and ceilings exposed. This eliminated 100,000 square feet of gypsum board, metal studs and painted assemblies. The project will deliver 242 metric tons of embodied carbon.
NRMCA Goals for 2030
From 2015 to 2030, the NRMCA seeks a 50 percent reduction in carbon emissions. Concrete’s carbon footprint is already down 13 percent in the first five years. Fortunately, there are ways to further reduce CO2 emissions in cement production.
Fuel savings and changes in cement kilns
Reducing calcination and offsetting it are common sustainability goals throughout the industry. One goal is to reduce the use of fossil fuels in operating cement kilns. Forty percent of the industry’s emissions come from heating limestone in coal-fired kilns. Calcination requires 2700-degree F temperatures. The other 60 percent is CO2 released as limestone breaks down into lime (calcium oxide). Fueling kilns with renewable energy is one answer. The possible electrification of kilns is another.
Cementa, a Swedish cement producer, seeks to electrify cement kilns. A feasibility study will determine whether its plasma technology is a viable alternative. Wind turbines would reduce the carbon footprint even further.
It is possible to increase the use of waste materials and decrease the use of fossil fuels in kilns. Examples include wood, agricultural waste and car tires. It may also be possible to fire cement kilns using hydrogen-based fuels.
Another way to reduce carbon emissions is to produce cement at lower temperatures. Limestone calcined clay (LC3) cement is one example. Since it works at much lower temperatures, clay calcination requires about 55 percent less energy than clinkerization. The use of lower-grade clay and limestone is more eco-friendly.
Clinker and energy savings
It is also possible to reduce the environmental impact of concrete by reducing clinker. It’s already been reduced from 90 percent in 1990 to as low as 65 percent today. Blended cements with less clinker reduce carbon emissions.
Calcium silicate cement: 70 percent less carbon
Research also continues into ways to make concrete a more effective carbon sink. Some newer products reduce carbon emissions in multiple ways. The International Cement Review discussed a calcium silicate cement with 70 percent lower CO2 emissions.
The formulation:
- Requires 20-30 percent less energy to produce
- Emits up to 30 percent less CO2 during calcination
- Consumes added CO2 during its special curing process
Supplementary cementitious materials (SCMs)
SCMs gobble up waste byproducts otherwise destined for landfills. Examples include slag cement, fly ash and silica fume. In South Africa, there’s an effort to harvest legacy fly ash deposits already in landfills.
CO2 Capture and Concrete Production
The search continues to find ways to capture and/or use more CO2 during concrete production. Carbon utilization in concrete has a promising future. The Center for Climate and Energy Solutions estimates it will be a $400 billion market by 2030.
CO2 injection
Classic CO2 sequestration is a little like the production of soda pop. This comparison leads to the fanciful question, “What would it take to sequester the world's CO2 in soda?” Believe it or not, someone has made the calculations. Quadrillions of cans!
At Iceland’s Hellisheidi Hydrothermal Power Plant, CarbFix captures CO2 and injects it into water. The company says the technology can “be applied for coal, gas, cement, steel and more.” Technicians pump the carbonated water into volcanic basalt 3200 feet deep. The basalt is rich in calcium and magnesium. Both minerals bind with the CO2 to form carbonates.
Carbon-cured cement
Why not take advantage of mineralization to strengthen concrete’s compressive strength? It is possible to inject CO2 into concrete where mineralization locks it up. Atlanta’s 725 Ponce de Leon Avenue project is one example. The project utilized 48,000 cubic yards of CO2-injected concrete. The structure diverts 1.5 million pounds of CO2 from the atmosphere. This is equal to the amount of CO2 absorbed by an 800-acre forest for a year.
Zero Carbon Emissions: The Holy Grail of Sustainable Production
Is it possible to develop a zero-carbon cement plant? Yes, although it requires a diverse suite of new technologies. You’ll find operating or at least planned pilot programs in Belgium, Norway and India. The Dalmia Cement project in India will use half-a-million tons of CO2 per year.
Learn More
Research and innovation continue to improve concrete’s sustainability throughout its lifecycle. Check out this video to learn more. The Pennsylvania Aggregates and Concrete Association (PACA) posts news about industry developments. We welcome your inquiries. Please contact us at your convenience.