Posted on June 02, 2022
When it comes to carbon emissions, calcination in cement kilns remains the industry’s greatest challenge. First, fossil fuels remain the primary source of the extreme heat required. Second, the decarbonization of limestone releases large amounts of carbon dioxide.
In the concrete industry and beyond, the quest for carbon neutrality requires nothing less than a technological revolution. Evolution is too slow; the need is too great. Fortunately, there are promising developments on the horizon.
Cement Kilns: Background
Cement kilns date back to the invention of Portland cement in 1824. It is named after Portland, England. In 1885, rotating horizontal kilns began to replace the original vertical, stationary kilns. Within five years, horizontal kilns dominated. In 1909, Thomas Edison received a patent for a long kiln almost double the length of previous designs.
Wet process
In wet-process kilns, a slurry containing about 40% water entered the apparatus at ambient temperatures. The inefficiency of heat transfer makes the process inherently inefficient. It simply takes too much energy to remove the moisture. Wet kilns can be more than 600 feet long and 18 feet in diameter.
In a semi-wet process, a filter press reduces the moisture content to conserve energy.
Dry process
The dry-process cement kiln is the most advanced and automated system on the market. This type of kiln is more thermally efficient in part because of the elimination of the evaporative step.
Dry kiln designs often include a preheater tower. The raw meal gets fed into the top of the tower. There, hot gas from the kiln directly heats it.
The large surface area of the finely milled particles makes the process quite efficient. About 30-40% of decarbonization occurs before the meal ever gets to the kiln. With the addition of a precalciner burner, it is possible to increase this to 85-95%.
The kiln is a long, slightly inclined cylinder that fully rotates every 1-2 minutes. The burner is at the lower end. Raw meal enters at the higher, cool end. The materials get dried as it proceeds toward the burner, It is also cooled using a high-efficiency cooler.
Kilns and alternative fuels
Today’s quest for more efficient kilns includes the use of alternative fuels. Fuel accounts for roughly a quarter of cement’s production cost. Researchers continue their decades-long search for cost-effective alternatives to fossil fuels.
Thus far, most fossil fuel alternatives come with disadvantages. High costs and inconsistent supplies are common challenges. Nonetheless, there are some promising alternatives to fossil fuels.
For example, it is possible to use biomass to fuel both wet and dry kilns. In California, S.B. 596 requires carbon-neutral cement production by 2035. One plant is already firing its kilns, in part, with pistachio shells. Textiles and plastics are other possible feedstocks.
The use of waste fuels reduces the industry’s carbon footprint. It also addresses the waste disposal problem. For example, the Norcem Brevik plant in Norway meets 70% of its fuel needs with waste-based alternatives. These include plastics, paper, textiles, and even hazardous waste.
One advantage of high-temperature cement kilns is their ability to destroy organic compounds. They also combine inorganic substances with traditional raw materials to produce clinker. Free lime in the clinker can absorb hazardous elements. Overall, it is an efficient process generating only minor amounts of solid residue.
There is another important advantage. Waste destroyed in cement kilns reduces the volume of material sent to traditional incinerators.
Using special equipment, it is possible to reduce wood construction waste to pieces suitable for incineration. A self-cleaning magnet removes nails before the material goes into the kilns. In California, Mitsubishi Cement experimented with a 50:50 coal and construction waste mix to fuel its kilns.
Electrified Kilns
Kiln electrification may also contribute to the industry’s pursuit of carbon neutrality. The goal is to substitute fossil fuels with low-emission electricity to decompose limestone. Carbon dioxide is more concentrated since it is not diluted by other flue gasses. This simplifies carbon capture.
The Institute of Materials, Minerals and Mining has constructed an electric kiln prototype. VTT Technical Research Centre of Finland came up with a gas-tight design about 40 feet long. The project lead cautions that scalability remains a question. More feasibility studies are to come.
Kilns and solar-sourced energy
In a few hours, the sun delivers more energy to the earth than the human race consumes in a year. Efficiently harnessing this infinite energy source remains the challenge.
Fortunately, powering kilns with solar heat is a more viable possibility than ever. At the same time, scalability and upfront capital costs remain important challenges.
For example, it is possible to use computer-controlled mirror arrays to concentrate solar energy at the top of a tower. Both Synhelion and Heliogen embrace this concept. Heliogen’s process for powering heavy industrial processes is called HelioHeat. Company officials at Synhelion claim the ability to produce the hottest existing process heat available via solar (1,500°C). The company also developed a zero-emission carbon capture technology to complement the process. CEMEX and Synhelion have collaborated to produce the world’s first “solar clinker.” An industrial-scale pilot plant is next.
Another option is to produce syngas from low-grade carbonaceous feedstock. High-temperature thermal reactions use CO2 and water to obtain hydrogen and carbon monoxide. These are the essential building blocks for synthetic fuels.
However, it does not advance the quest for carbon neutrality if fossil fuels are consumed in the process. As researchers at Sandia National Laboratories note, concentrated sunlight does. They’ve dubbed it the “sunshine to petrol” approach.
About PACA
The Pennsylvania Aggregate and Concrete Association (PACA) monitors the latest developments in the industry. We welcome questions about your next project. Please contact us at your convenience.
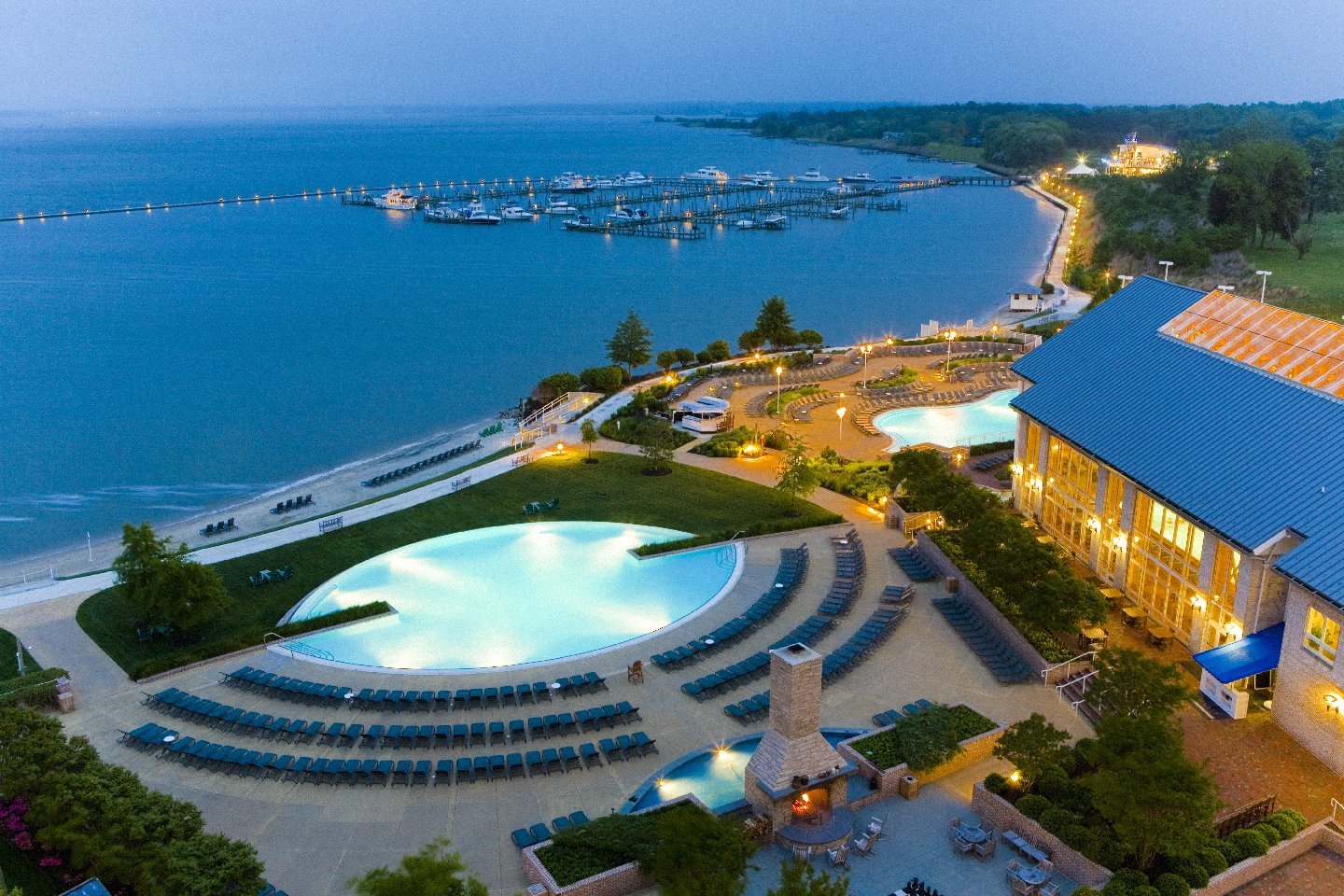