Posted on October 26, 2023
Insulated concrete form (ICF) construction has been around for decades. Despite this, lack of familiarity sustains myths in some quarters.
Nonetheless, ICF construction continues to expand. According to Global Market Insights, the ICF market will expand at a robust 6.4% CAGR through 2032. They project that North America will command 43% of that.
ICFs deliver an energy-efficient, resilient building envelope for three key reasons:
Structural integrity
Low air leakage
High insulation value
ICF construction also excels at wind, water, and fire resistance. Such structures stand up to natural disasters like hurricanes, tornadoes, floods, and wildfires.
ICF resilience and energy-efficiency are increasingly attractive as the atmosphere warms. Higher carbon dioxide levels are largely to blame. According to a NASA graph, CO2 concentrations increased from 317.58 ppm in March 1960 to 423.68 ppm in June 2023. Thatās a 25% increase. Ice core data reveals that concentrations never exceeded 300 ppm during the previous 800,000 years.
5 ICF Myths Busted
Growth in the ICF market would be stronger if but for certain myths that perpetuate to this day. Here are five common ICF myths.
Myth #1: ICFs are too expensive
ICF construction is increasingly cost-competitive. As energy costs rise, ICF energy savings increase. Also, more refined and efficient construction techniques deliver more value. ICF longevity enhances lifecycle savings. Finally, intangibles like sound attenuation merit consideration.
ICFs deliver a building envelope that reduces mingling of conditioned and unconditioned air. Compared to wood-frame construction, energy savings of 50% or more often accrue.
Consider the savings when energy bills are reduced by half. For example, the U.S. Energy Information Administration (EIA) estimates that a typical Pennsylvania household uses more than 10,000 kilowatt-hours (kWh) of electricity every year. This leads to energy bills averaging more than $2,000/yr. In constant 2023 dollars, 50% savings ($1,000/yr) add up to $30,000 over the life of a traditional 30-yr mortgage.
Thereās also the potential for reduced maintenance costs, long-term. Insurance savings are also possible. However, this is more likely from carriers specializing in ICF homes. ICF construction promotes savings in areas prone to flooding, wildfires, tornadoes, and hurricanes.
Myth #2: ICFs are only for residential foundations
It is true that āICFs were first developed as a below-grade foundation wall forming system,.ā However, above-ground use quickly expanded. Today, you'll find ICFs used for multi-family mid-rises, schools and universities. Other uses include military projects, houses of worship, and theaters. ICF high-rises have topped twenty stories.
Energy-efficiency and longevity are a potent combination. Every dollar saved per month equals $360 over the life of a 30-year mortgage. That's $1,200 over the 100-year life of certain commercial ICF structures.
ICFs work well with energy-efficient windows and shades. Architect Magazine notes that there are fiberglass and vinyl windows rated from R-5.9 to R-11.1. Some of these feature argon gas-filled, triple-glazed construction. Energy Star lists windows with U ratings as low as 0.12. Motorized insulated window shades also complement energy-efficient ICF construction.
Myth #3 : thereās a risk of blowouts
In the early days of ICF construction, blowouts were sometimes a concern. It is true that pouring too much too quickly, or without proper reinforcement, can still cause blowouts.
However, when concrete is poured according to spec, blowouts are rare. Refinements in ICF training and installation also reduce risk. Insulated concrete forms typically hold fresh pours at a max rate of four feet per hour. Typical placements are in the neighborhood of nine to 13 feet per day.
Myth #4: cavity walls are competitive
In fact, the thermal performance of ICF walls is typically superior. This is due their thermal mass, continuous insulation, and airtightness. International codes recognize important differences between traditional cavity and ICF walls.
One test compared an R-23 ICF wall and an R-20 wood-framed wall after they reached steady state. The R-20 wood wall actually performed at R-14.8, while the R-23 ICF wall actually exceeded its nominal rating, performing at R-23.36.
Myth #5: thereās resistance to downsizing the HVAC system
A key advantage of ICF construction is downsized HVAC and reduced operating costs. You want to take full advantage of airtight thermal mass ICF walls.
HVAC contractors are often wary of customers complaining that their systems cannot handle cold blasts or heat waves. With ICF construction, they may go with traditional calculations long-used for wood-frame designs. This may lead to oversized HVAC systems in ICF buildings. Capital costs increase, and heating/cooling inefficiencies result.
Contractors should account for the insulating properties and thermal mass of ICF walls. It is vital that the energy model accounts for reductions in HVAC loads. Some energy modeling programs do not account for the real-world performance of ICFs. They may input higher leakage rates into their calculations, for example.
Despite myths to the contrary, ICF construction is proven, cost-effective, and long lasting. It is widely deployed in an array of residential and commercial applications. Testing reveals how ICF energy-efficiency greatly exceeds that of traditional cavity walls. Savings of 50% and more multiply over the life of the structure.
About PACA
The Pennsylvania Aggregates and Concrete Association (PACA) uses this website to inform its members and the general public of the latest industry innovation. The team at PACA welcomes your questions about your current or upcoming concrete projects. Please contact us at your earliest convenience.
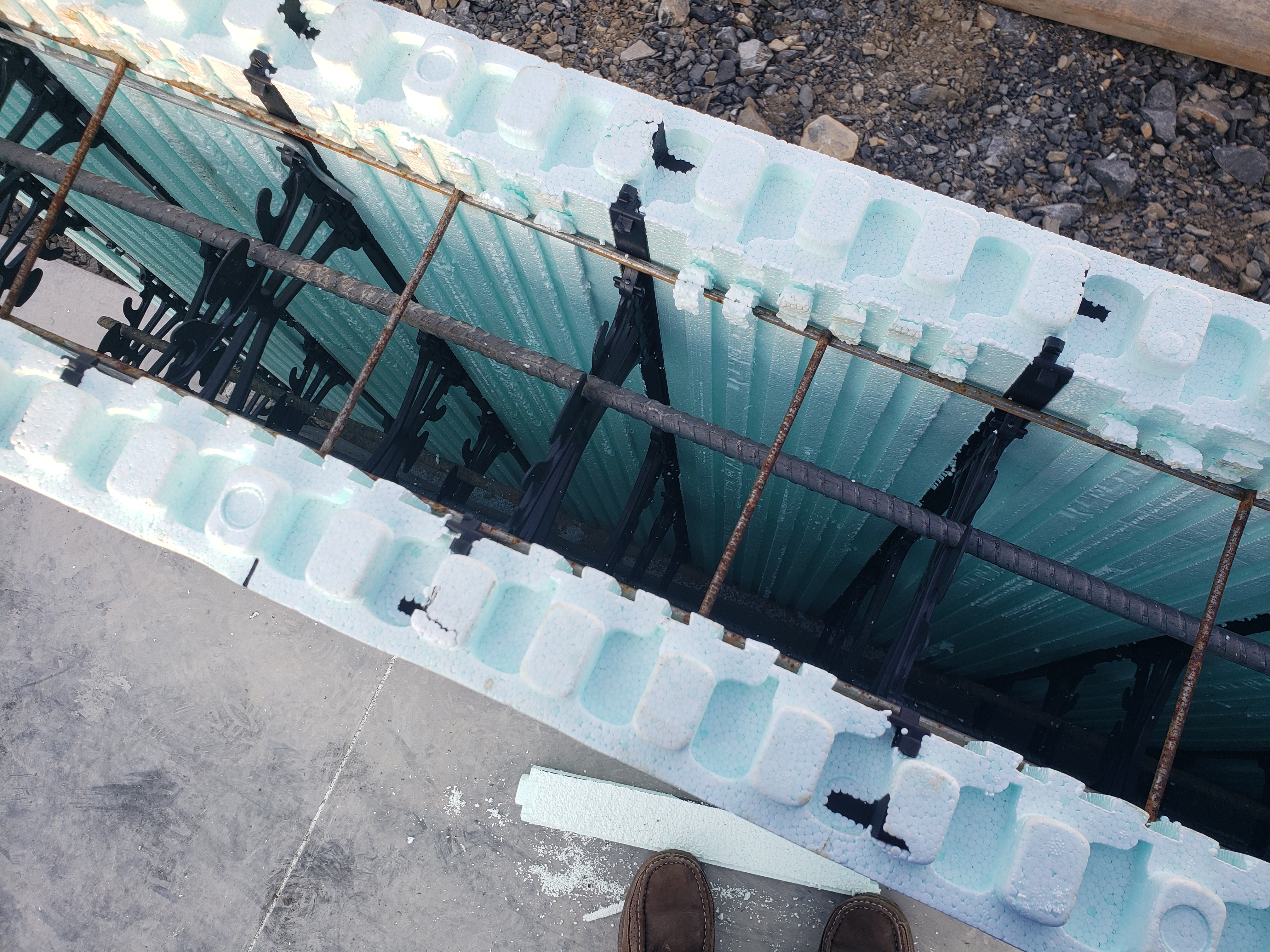