Posted on January 26, 2023
Emissions are a major concern when cement kilns are fired with fossil fuels. One potential alternative is green hydrogen. However, for hydrogen to be “green,” it must be produced using renewable energy.
Traditional hydrogen production is energy-intensive. Now, a new photocatalyst may be a game changer. Green hydrogen derived from ammonia is a real possibility.
Why Hydrogen From Ammonia?
Ammonia (NH3) is a carbon-free molecule with a very strong N-H bond. To get affordable green hydrogen, researchers must find a more energy-efficient way to break that bond. A new low temperature process delivers in that regard.
While ammonia is caustic in concentrated form, industry experts routinely handle it safely. Why is ammonia such a good hydrogen carrier? Compared to pure hydrogen, ammonia is more easily compressed, transported, and stored. It is stable at normal temperatures and pressures.
Current technologies crack ammonia to get hydrogen and release nitrogen. The big drawback is temperature. The endothermic reaction requires temperatures of 650-1,000 °C. It also uses expensive thermal catalysts like ruthenium, a rare element that is quite expensive.
Breakthrough Technology
Rice University researchers have identified a new way to obtain hydrogen from ammonia. They use an LED-powered device to facilitate a photon-driven reaction. Rather than ruthenium, the system uses copper and iron – cheap and abundant materials. The photon-driven catalyst operates at lower temperatures, yet it is as efficient as traditional thermal catalysts.
Researchers first conceived of antenna-reactor plasmonic photocatalysts more than 30 years ago. How do they work? Nanoparticles of catalyst are dotted with tiny clumps of "antenna" material that absorb light. The particles absorb energy from LEDs to free up short-lived "hot electrons." There is sufficient energy to start a chemical reaction at ambient temperatures.
The photocatalyst separates hydrogen from nitrogen using iron as the reactor. Copper is the light-collecting antenna. This approach produces results that are competitive with traditional methods. Researchers report that, "under illumination, the copper-iron showed efficiencies and reactivities that were similar to and comparable with those of copper-ruthenium."
Commercialization Underway
Commercialization of green hydrogen requires methods that are far less energy intensive. An ammonia-splitting reactor from Syzygy Plasmonics may be a viable solution. “Photon-driven chemistry represents a new frontier that is changing chemical engineering and manufacturing,” says Suman Khatiwada, Syzygy co-founder and CTO.
Syzygy uses LEDs in an ammonia-splitting reactor with 500 times the volume of Rice’s initial laser-based set up. The compact device is the size of a small washing machine. Thanks to the low-temperature, low-pressure environment, it is possible to use simple materials like aluminum and glass to build the devices.
Syzygy's demonstration reactor processes about a ton of material per day. Stacking increases output. Its reactors use light instead of heat to electrify chemical manufacturing.
Ideally, the reactors are powered by renewable electricity to reduce emissions even further.
Implications for the Cement Industry
In the cement industry, the dream is to power kilns with green hydrogen. Firing kilns with green hydrogen could usher in an era of emissions-free production of Portland cement. Success requires a further step - the capture of CO2 released during calcination. The key lies in producing green hydrogen that is at once affordable and plentiful. Thanks to the work at Rice University, sourcing it from ammonia is now a more viable possibility.
Interestingly, hydrogen is already helping to fuel cement kilns around the world. For example, Cemex uses hydrogen as a catalyst in kilns at its European plants. It now plans to do the same at four plants in Mexico and one in the Dominican Republic. Mexican cement. Hydrogen injection enhances the combustion process while reducing the use of fossil fuels. Cemex wants to work toward making hydrogen the primary fuel source in cement kilns.
Green hydrogen competes with oxyfuel and electrification in the quest for more eco-friendly kiln operations. A 2022 University of Pennsylvania study discusses how cost remains an obstacle with both oxyfuel and electrified options. As the author of the study asserts, “Economic hurdles are one obstacle to oxygen-fired and electric cement furnaces becoming reality at cement plants that emit high amounts of CO2."
Future Sources of Green Hydrogen
In the future, there may be other ways to obtain green hydrogen at an affordable cost.
High-efficiency electrolyzers
One is to make freshwater electrolyzers more efficient. For more than a century, efficiency ratings have been stagnant in the 70-75% range. One challenge is the "bubble problem." Non-conducting bubbles get between the electrodes and the electrolyte fluid, reducing efficiency.
Now, a new design addresses this long standing problem. Hysata’s patented capillary-fed electrolyzer keeps the electrolyte away from the anode and cathode. As a result, bubbles no longer inhibit the process. The capillary-fed design reportedly achieves 95% efficiency.
Hysata’s cell design eliminates the need for expensive cooling. Electronics are cost-efficient and grid-friendly. Simplified operations make it easier to automate and scale. Modular tech uses the same basic building block for MW and GW installations.
Thanks to the capillary-fed design, Hysata estimates that hydrogen costs could drop as low as $1.50/kg in several years. It projects gigawatt-scale production by 2025.
Seawater electrolysis
Current hydrogen production requires freshwater electrolysis. However, freshwater is a finite resource coveted for other vital uses. Seawater electrolysis is an alternate answer. However, corrosion is a major obstacle.
Now, researchers claim they’ve designed a seawater electrolyzer that works as efficiently as freshwater designs. And, there’s an interesting byproduct that builds value. The process can also produce lithium.
Researchers overcame the corrosion problem using an ingenious evaporation technique. Nanjing Tech University researchers report their seawater electrolysis machine operated for 133 days.
The key is the use of waterproof, breathable PTFE-based membranes. They keep the seawater separate from the potassium hydroxide electrolyte. Water vapor passes through them, but they prevent liquid water from getting through. The membrane blocks all ions that might otherwise damage the electrodes.
Vapor pressure differences drive the system. Evaporation occurs on the seawater side. Spontaneous seawater gasification delivers hydrogen at 71% efficiency. Development is still in its infancy. The proof-of-concept prototype generated enough hydrogen to power a car for two miles.
About PACA
The Pennsylvania Aggregates and Concrete Association (PACA) reports on the technological innovations impacting the industry. Our team welcomes questions about your current or upcoming concrete project. Please contact us today!
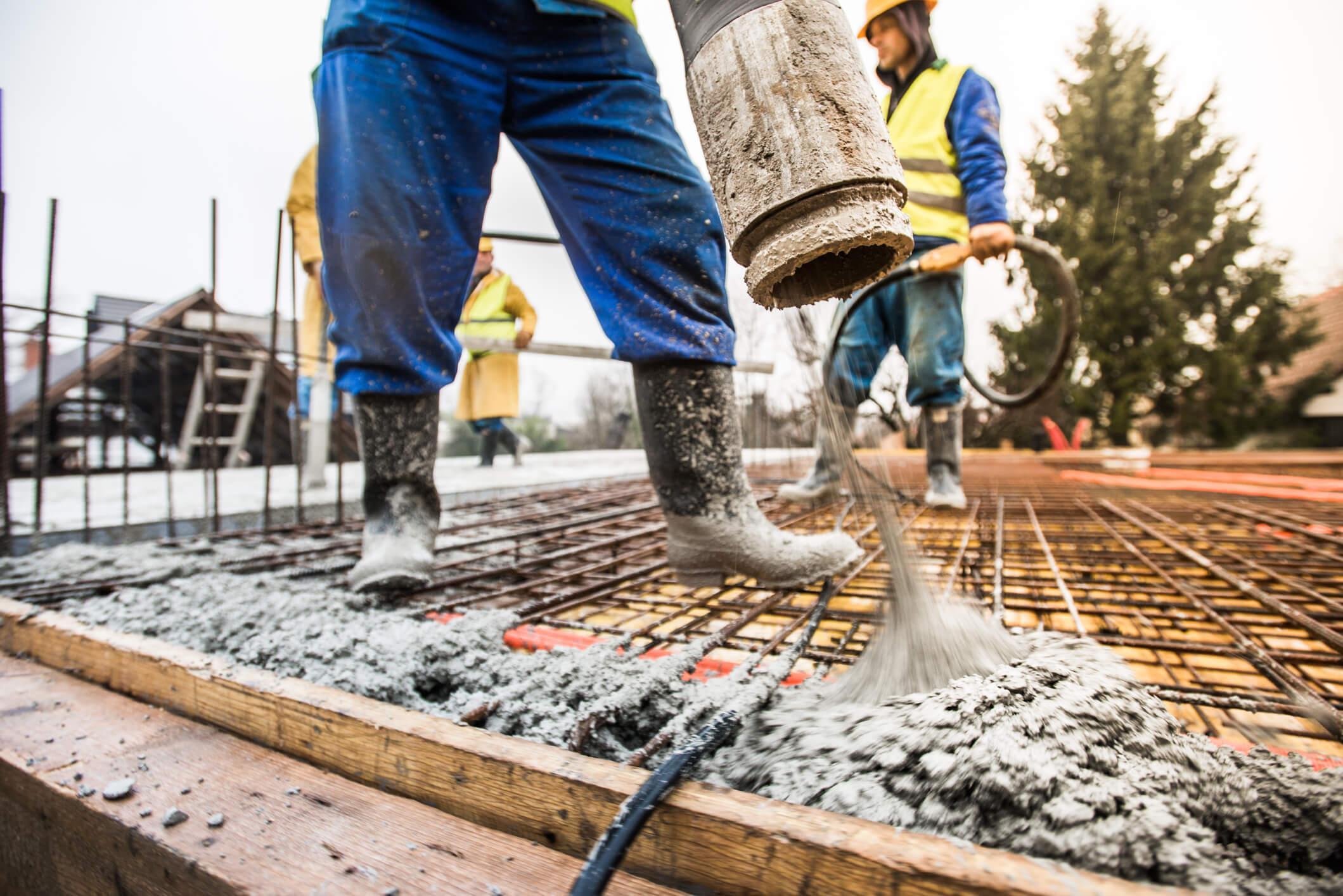