Posted on February 03, 2022
According to the U.S. Environmental Protection Agency (EPA), construction and demolition (C&D) waste totaled 600 million tons in 2018. Demolition accounted for about 90% of the total, while construction accounted for about 10%. 455 million tons of C&D debris went to “next use.” 145 million tons went to landfills.
Around the world. construction and demolition waste is big business. One projection shows the global C&D waste market growing from $108.74 billion in 2021 to $142.92 billion in 2028. There is a massive disparity in rates of C&D waste recycling. It is more than 90% in Italy and the Netherlands, for example, but less than 10% in Finland and Greece. In Brazil, the recycling rate is 1%.
A lot of this waste is concrete. Recyclers crush and process some of it to produce recycled concrete aggregate (RCA). It is not always necessary to crush the concrete to reuse it. Broken slabs may line ditches to reduce erosion, for example.
RCA: Inherent Limitations
At present, it is not practical to use RCA instead of natural aggregate (NA) in most construction projects. There are two key obstacles. First, RCA absorbs moisture at a higher rate. Second, excess quantities of adhered mortar may compromise performance. Porous adhered mortar weakens the bond between old and new concrete matrices. In fact, the compressive strength of RCA concrete is about 10-30% less than with OPC.
Previously, studies demonstrated that graphene additive improved compressive and tensile strength in concrete made with natural aggregates. Now, research shows that graphene oxide can deliver NA-level performance in RCA concrete. Other nanotechnologies show promise in improving durability and mechanical strength. Examples include carbon nanotubes and carbon nanofibers. However, graphene oxide is far more affordable.
RCA: Supply and Demand
At present, recycled crushed concrete accounts for about 5% of all aggregate. About two-thirds of RCA becomes road base. Another 9% goes into asphalt, while 6% is used in new concrete mixes. Therefore, there’s ample opportunity to redirect RCA supplies to new concrete mixes. It simply needs to sufficiently perform to make it a viable alternative.
Supplies of crushed concrete vary across the country. In some areas, supplies are fully recycled. For example, the Florida Department of Transportation (FDOT) says that “all the crushed concrete that is produced in the state is currently being utilized.”
The FDOT also sounds a word of caution. The quality of crushed concrete varies “depending on where it originates and how it is processed.” It is also vital that RCA does not contain toxic contaminants like asbestos or lead.
The cost to transport aggregate is also a consideration. A local RCA source might compete favorably with natural aggregates coming from further away. However, using local RCA requires a local ready-mix plant capable of handling it.
Graphene Enhances RCA Properties
Graphene continues to secure its status as a modern-day miracle material. Imagine one substance used in everything from batteries to lubricants, and from superconductors to body armor. It can also strengthen concrete. This should not be surprising, given that it is 100 times stronger than steel.
Previous research focused on graphene oxide (GO) added to concrete with natural aggregates. There is now a study that examines the use of a graphene additive with RCA. Is it possible to replace NA with RCA? This research answers, “Yes!” Relatively small amounts of GO in RCA concrete deliver the performance required.
Researchers examined a variety of concrete mixes. The control mix was 70% ordinary Portland cement (OPC) and 30% fly ash. Other mixes featured 100% RCA. They also included 0.0, 0.05 and 0.10% graphene oxide.
The team determined that an RCA mix with just 0.1% graphene oxide (GO) and balled-milled graphene oxide (GObm) replicated the mechanical and durability properties of the control mix. The RCA mix also had a better economy index and higher overall desirability function. Increasing graphene levels improved compressive strength, electrical resistivity and ultrasonic pulse velocity. Increasing graphene also reduced sorptivity and initial surface absorption.
Graphene Supplies
Of course, RCA concrete with graphene requires reliable GO supplies. Unfortunately, volume production has been lacking to this point. An article published by the Institution of Mechanical Engineers asserts that, “The biggest challenge for many graphene producers has been delivering consistency of quality and supply volume.”
First Graphene Ltd. has found success in addressing these quality and supply challenges. It uses a proprietary electrochemical exfoliation process to produce high-purity graphene. First Graphene found a way to overcome the problem of agglomeration. It uses “water-based admixtures containing pre-dispersed graphene nanoplatelets.” In December 2021, it filed for a patent in the UK to protect its process.
First Graphene’s R&D center is at the University of Manchester in the UK. Its initial production facility is in Australia. The plant can produce 100 tons of high-purity graphene per year. Management asserts that it is possible to replicate and scale the plant at other locations around the world.
Conclusion
Aggregates constitute about 60-80% of a typical concrete mix. Now, research shows that it is possible to replace natural aggregates with RCA, as long as a relatively small amount of graphene is added. Long term, the viability of RCA concrete may also lead to more recycling of concrete. Specifying RCA concrete may also give companies another way to achieve their sustainability goals.
About PACA
The Pennsylvania Aggregates and Concrete Association monitors new developments in the industry. This includes research into the sustainability of concrete. For help with questions about your upcoming concrete project, please contact us.
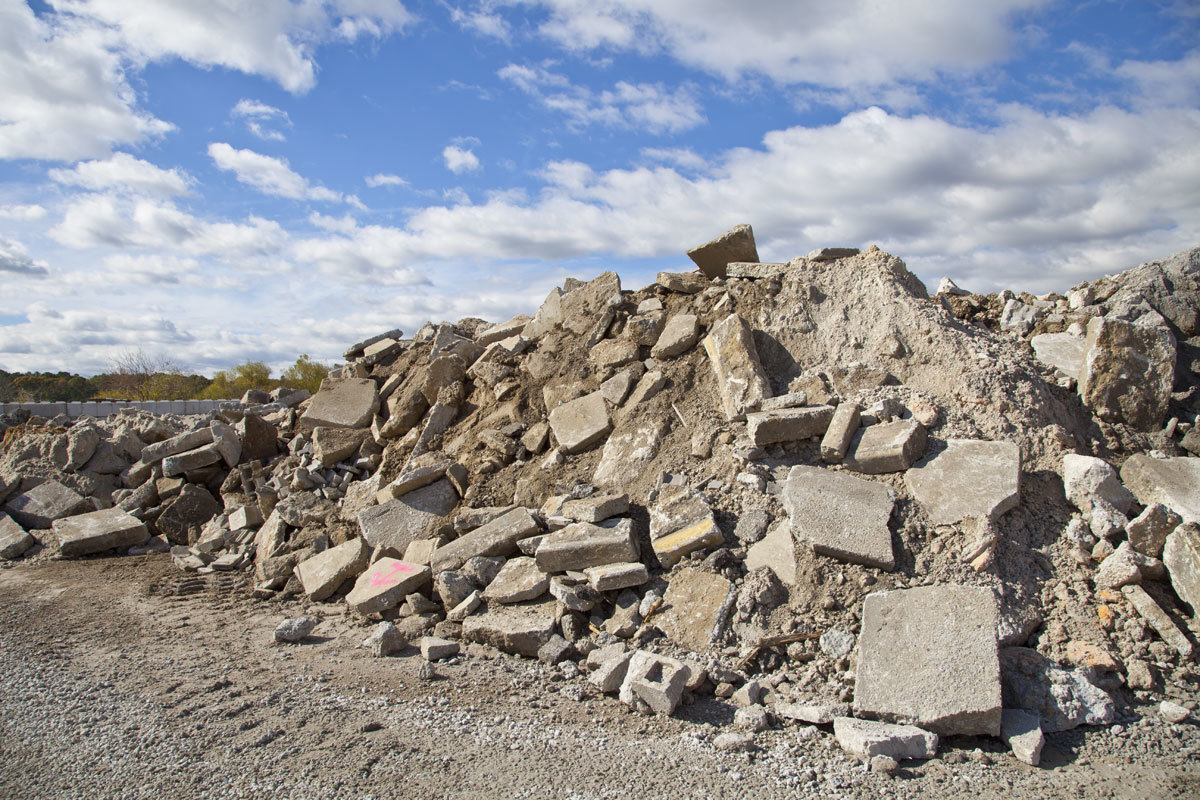