Posted on September 16, 2021
Global greenhouse gas emissions were consistent for the first four decades of the 20th century. Today’s levels are about 10 times that. According to the EPA, 65 percent of these emissions come from fossil fuels and industrial processes.
Today's concrete industry stands at the intersection of unprecedented demand and aggressive emissions goals. As it faces greater pressure to cut emissions, it will also benefit from new infrastructure initiatives.
Concrete is the most abundant man-made material. Contractors place 30 billion tons every year.
The most energy intensive part of concrete's supply chain is cement production. Annual cement production is 4.1 billion tons. Every ton requires three to four gigajoules (GJs) of thermal energy to produce. Much of that energy comes from fossil fuels. A joule is the amount of energy required to send one ampere through one ohm of resistance for one second. One gigajoule equals 277.8 kWh, or approximately 0.17 barrels of oil.
Due in large part to its reliance on fossil fuels, cement production accounts for more than a quarter of all industrial CO2 emissions.
Decarbonizing the concrete industry requires a long-term, multi-faceted commitment. Progress is a must in every area:
Improved energy efficiency
Use of waste and biomass as fuel
Carbon capture, storage and utilization (CCUS)
Decarbonization of transportation and electricity
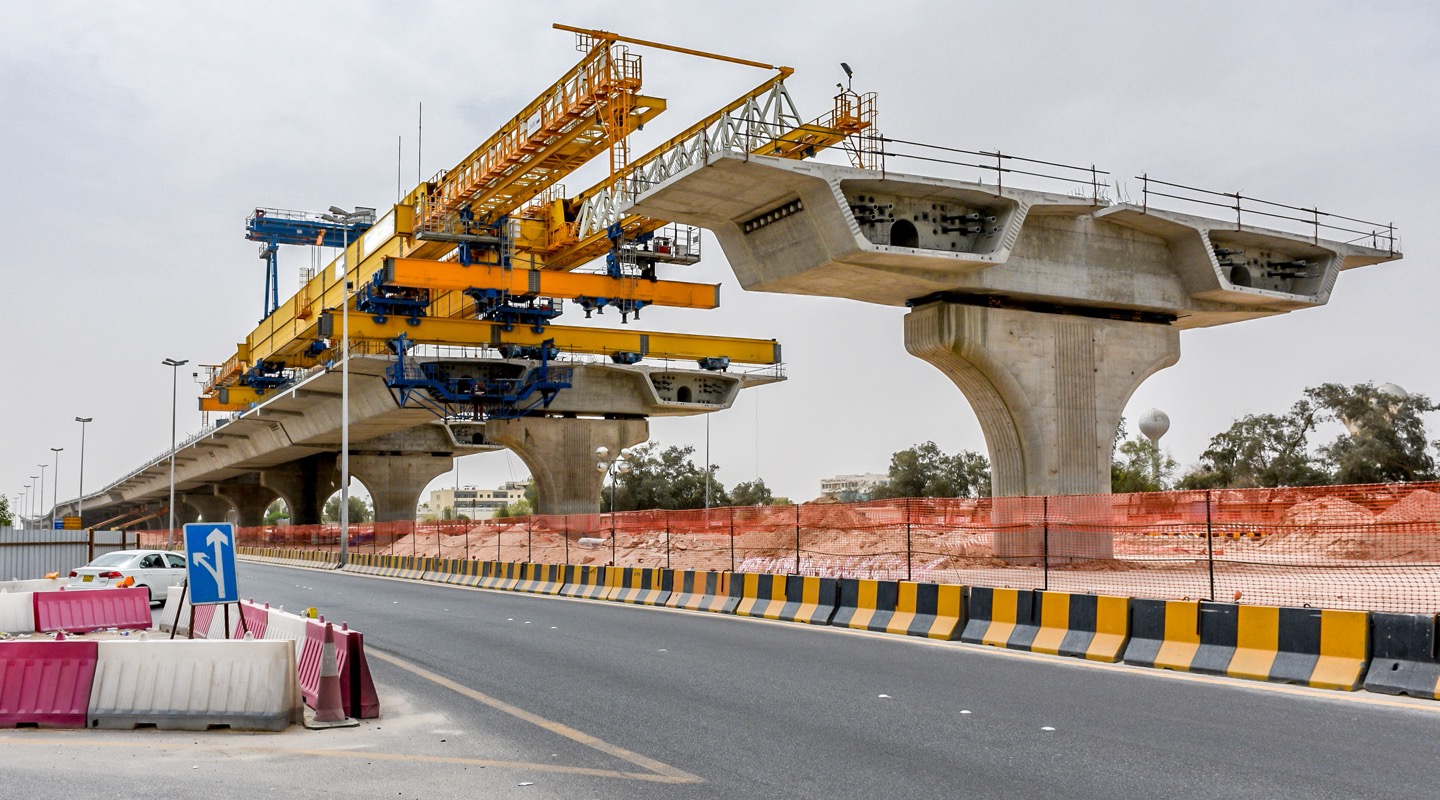
Government Initiatives
Federal government projects account for half of the domestic concrete market. This means there’s a degree of government leverage over industry emissions initiatives. Green procurement is one part of the current administration’s comprehensive infrastructure proposal. As the White House says, “The government can exercise its procurement power to support early markets for these very low- and zero-carbon industrial goods.”
At the Leaders Summit on Climate, the United States said it seeks to reduce carbon emissions by half for the period 2005-2030. It seeks 100 percent carbon-free electricity by 2035. It wants to achieve net-zero emissions by 2050.
Evolution of Carbon Removal and Reduction Tech
One key to low-carbon concrete is reducing the carbon footprint of all components. Not just cement, but aggregates, gypsum and SCMs as well.
The Global CCS Institute highlights the value of bioenergy with carbon capture and storage (BECCS). It sees BECCS as one of the best ways to decarbonize emission-intensive industries. However, success requires reliable sources of biomass and enhanced scalability.
Existing technologies can reduce concrete’s lifecycle CO2 by 40 percent. Net-zero concrete is only possible when additional steps occur, like:
Kilns fired with biogenic fuel from sustainable sources.
Waste heat used for added carbon capture.
Optimized carbonation of demolished concrete.
CO2 injection offers double benefits. One, it permanently sequesters carbon. Two, it increases concrete's strength so less is needed.
The UNFCCC Paris Agreement seeks to keep global warming to well under two degrees Centigrade. It is ideal to keep it as close to 1.5 degrees as possible. To achieve such goals, it is insufficient to simply reduce emissions. It is necessary to actually remove CO2 from the atmosphere.
Carbonating rock aggregate
Blue Planet’s technology utilizes CO2 from flue gas. It generates material for fabricating carbonate rocks for use as an aggregate. This material becomes a substitute for quarried limestone. Most carbon capture methods include an energy-intensive purification step. Blue Planet’s does not.
Carbonating concrete
CarbonCure injects precise amounts of CO2 from pressurized tanks into concrete mixes. This produces nanoscale calcium carbonate that simultaneously sequesters carbon and builds strength.
Biomass for Energy
In Norway, a Norcem plant gets as much as 30 percent of its energy from biomass. There are also plans to capture up to 400,000 tons of CO2 per year for transport to a North Sea storage site.
Officials at a Lafarge cement plant in Ontario have also explored the use of biomass fuel. The company planted 2,500 acres of perennial crops for fuel. They estimated a 90 percent reduction in emissions compared to the use of coal and petroleum coke to fire the kilns.
Hydrogen fuel from clean sources
Compared to natural gas, hydrogen from clean sources is an ideal fuel. Water is the only emission. Green hydrogen reduces the carbon footprint of ground granulated blast furnace slag. This lowers the carbon footprint of concrete by reducing cement volumes. The resulting concrete is whiter and more reflectant. It is also stronger than ordinary Portland cement (OPC).
Hanson UK and Swansea University researchers have developed a green hydrogen demonstration unit. It is at the Regen GGBS plant in Port Talbot, Wales.
Composite gypsum binders
A 2020 study explores the potential of sustainable low-carbon binders. Gypsum binder is low-carbon, but it lacks compressive strength and water resistance. Composite gypsum binders seek to address these concerns. The researchers observe that, “Combining different types of binding substances allows production of strong and water-resistant low-carbon dioxide emission composites.”
For example, a mix they call hempcrete features gypsum composite binders. It is “sustainable, heat-resistant, humidity-free and carbon negative.”
Increasing natural carbonation
Natural carbonation is a slow process, mitigating its value in CO2 remediation efforts. However, every strategy to reduce atmospheric carbon is worthwhile to some degree.
Limestone (CaCO3) produces calcium oxide (CaO). In unsealed concrete, CaO reabsorbs CO2 from the atmosphere. This natural process offsets approximately one-fifth of the CO2 emitted during cement production. Keep exposed concrete unsealed to promote natural carbonation.
It is also advantageous to leave demolished concrete exposed for a period of time. Concrete demolition vastly increases the surface area of the concrete exposed to the air and humidity. This increases carbonation. It is ideal to crush concrete and to leave it exposed to air and humidity for several months. At present, this is only happening one percent of the time.
About PACA
SpecifyConcrete.org is a website of the Pennsylvania Aggregates and Concrete Association (PACA). The association uses this site to report industry developments to industry members and the general public. For more information, please contact us.