Posted on October 19, 2023
There are literally thousands of materials used in 3D printing. They also come in various forms: filaments, pellets, powders. resins, wires, pastes and gels. But, what if grout or a high-performance concrete mix poured forth from the nozzle? Well, it already is! 3D printed concrete (3DPC) is already making its presence felt. In fact, some analysts think it will become a billion-dollar industry by 2030.
3DPC: How it Works
In 3DPC, the printer nozzle’s path is pre-programmed via AutoCAD, SolidWorks, or similar programs. Material is laid down one layer at a time. For the sake of structural integrity, these layers must dry into a single homogenous unit. In the right applications, 3D concrete printing is quick, accurate, and efficient. Accordingly, it can reduce labor expenses. To fully realize prospective gains, training, monitoring, and precise mixing are essential.
One of the strengths of 3DPC is its integrative nature. It weaves everything together, from structural performance and geometric modeling to material preparation and construction. Green building initiatives also drive the growth of 3DPC. Construction waste, and therefore landfill impact, is minimal. The range of possibilities is impressive. 3D concrete printing can deliver inexpensive housing. It can also tackle intricate building designs common in upscale projects.
3D Printed Concrete (3DPC): Developments
The 3DPC industry is expanding as it gains acceptance across the construction industry. It’s also growing because innovators continue to attempt novel applications.
Wind turbine bases
General Electric already uses 3D printing to create metal parts for jet engines. Now, it intends to use high-performance concrete to 3D-print wind turbine bases. These resilient, relatively lightweight bases “could add as much as 80 meters – and possibly more – to the turbine’s height. Experts estimate that taller installations could increase output “by as much as 30%.
Equestrian barn
A 10,105 sq ft equestrian barn in Wellington, FL, is now one of the largest 3D printed structures on the planet. The $3 million facility features 16 stalls and a 2,100 sq ft circular, motorized horse walker. Florida-based Printed Farms used a COBOD BOD2 printer on the project. It features a steel truss framework that is readily sized up or down. To print a structure, polymer-fortified M68 Laticrete gets mixed with water and pumped to the printhead.
Printed Farms points to important advantages of 3D concrete printing. These include resilience, up to 100-yr longevity, minimized waste, and reduced labor. The equestrian barn was quite a step up for a company that printed its first home in 2021. That was a 1,525 sq ft residence in Tallahassee, FL.
The “Mighty House”
The Mighty House concept features 3D-printed wall panels and roof components that ship flat to the job site. There, workers quickly bolt them together. Materials went through rounds of fire, water, and structural testing prior to approval.
Project Olympus
Finally, consider Project Olympus, a project of Texas-based ICON. Engineers want to 3D-print structures on the moon using the 3,400-degree heat of a plasma torch to bond dust and rock fragments.
3DPC Challenges
In many ways, 3DPC is still an embryonic construction method. Several factors currently inhibit wider adoption.
Building codes slow to accommodate 3DPC
3DPC project developers often face a protracted approval process.
This is due in part to the fact that it often takes time for new construction tech to get incorporated into codes. 3D concrete printing is certainly no exception. Sometimes, 3DPC runs afoul of existing codes. For one project, 3DPC could not address code requirements for horizontal rebar.
The hurdles faced by 3DPC are analogous to those faced by mass timber construction. Challenges will resolve over time as this construction technique works its way into the building codes. As Printed Farms founder Jim Ritter sees it, “The more people print, the faster it becomes codified, the faster it becomes mainstream.”
Large build areas require massive printers
Expandable steel trusses create a sturdy framework from which the print nozzle can work its wonders. There are limits as to how large the framework can get while remaining cost-effective.
Inadequate interlayer bonding
It is inherently difficult to incorporate reinforcement into automated 3D concrete printing. Inadequate bonding between adjacent layers impacts the mechanical properties of printed buildings. As one researcher notes, “The layers introduce anisotropy and reduce the capacity to resist tensile and shear loads.”
Now, researchers propose the strategic insertion of U-shaped nails during printing. Two mm U-nails bridge the interlayer surfaces. The dowel effect increases both tensile strength (145%) and shear strength (220%).
Market Forecast for 3D Concrete Printing
According to Market Research Future, the global 3D concrete printing market is projected to grow at at a 55.60% CAGR, reaching $978.5 Million by 2030. For perspective, consider that the global ready-mix market is expected to reach about $900 billion by then. This means that, seven years from now, the 3D concrete printing market will be less than 1% of the ready-mix market.
The Future of 3D Concrete Printing
More advanced robotic technologies will eventually increase 3DPC's precision and efficicacy. It will deploy more sustainable materials, including fiberglass-reinforced geopolymers. Finally, as size constraints diminish, a new array of infrastructure applications will emerge.
About PACA
The Pennsylvania Aggregates and Concrete Association (PACA) uses this website to inform its members and the general public of developments in the concrete industry. The team at PACA welcomes any questions you may have about your concrete project. Please contact us at your convenience.
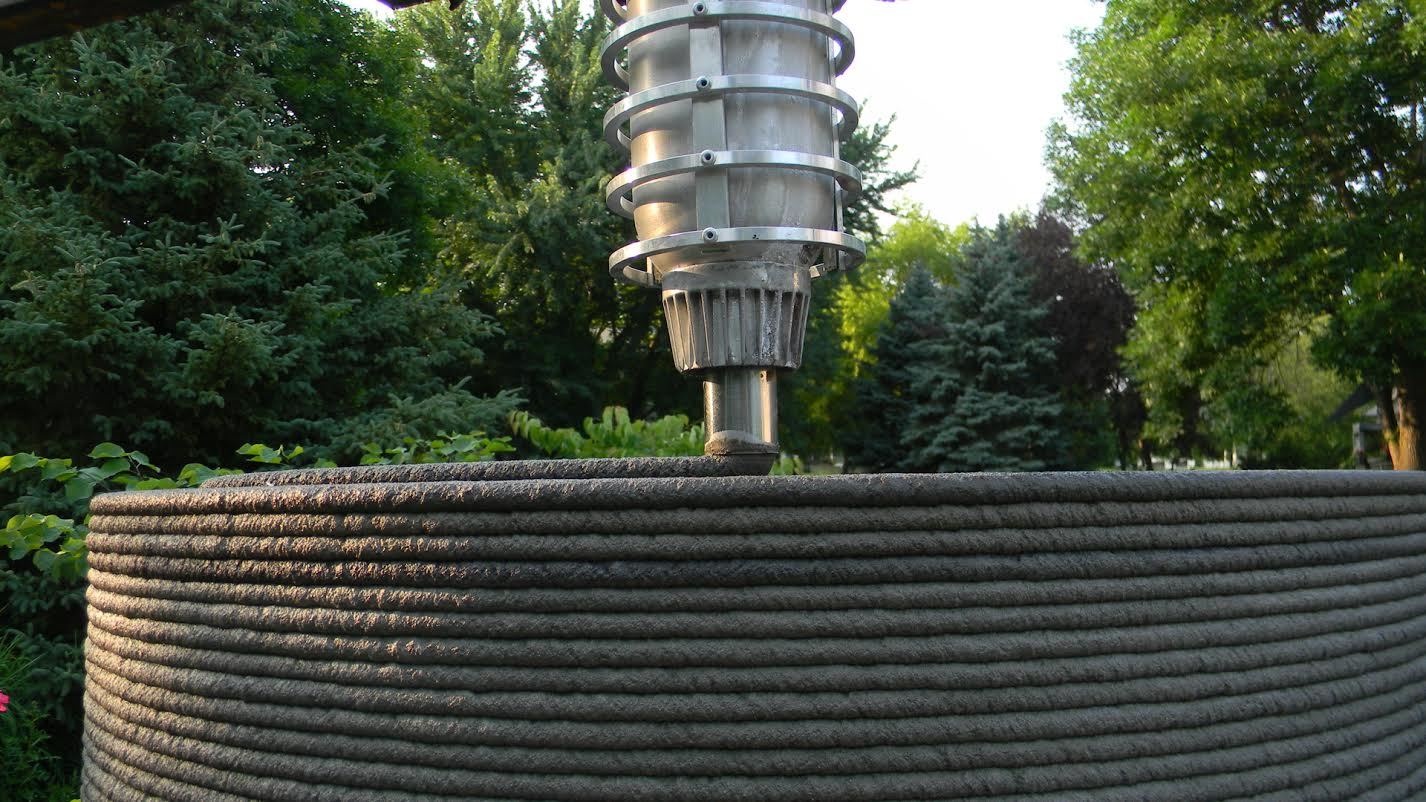